How common is this lightening foam core wings
#1
Banned
Thread Starter

Hello ,
I have a small home shop with hot wire cutter, vacuum bag where I build planes my own - nothing high tech, so I build small fun planes up to 1200mm wingspan I used to make wings out of foam core and blasa sheeted.
Anyway they were always little havier than balsa build up wings.
My last plane is 1040mm wing span and tried lightening, cutting out space and living 1/2 inch ribs and contours.
The plane is small so I added no spars inside and the sheeting is 1mm thick.
After lightening I cover it with solar film (I'll provide picture later) and the weight of one panel covered ended up ~65g so 130g / full span wing.
The way I do is:
- cut the wings carefully. Result is there are no big gaps or waves. Sanding is very light.
- Prepare wing joint tube ( usually made of 2-3 layers of 48g FG and wetted with waterbased varnish - it-s strong enough and very light after cures)
- Prepare well selected balsa sheets (light), put them them together with blue tape
- Apply carefull light layer of PU glue both sides balsa and foam core. Really carefull with the glue quantities. I use light and struggle to see, make sure is wet everywhere then spray little water.
- Put the sandwich together carefully
- In the vaccum bag for 2-3 hours
- Cut out foam between ribs ( 10-15mm) and other reqired contours for servo or other required
- Cover the wing with Solar film
My question is how other people do their foam core wing for small plane, are there other building techniques using foam core for light wings?
What can I improve to get even lighter wings?
Thanks,
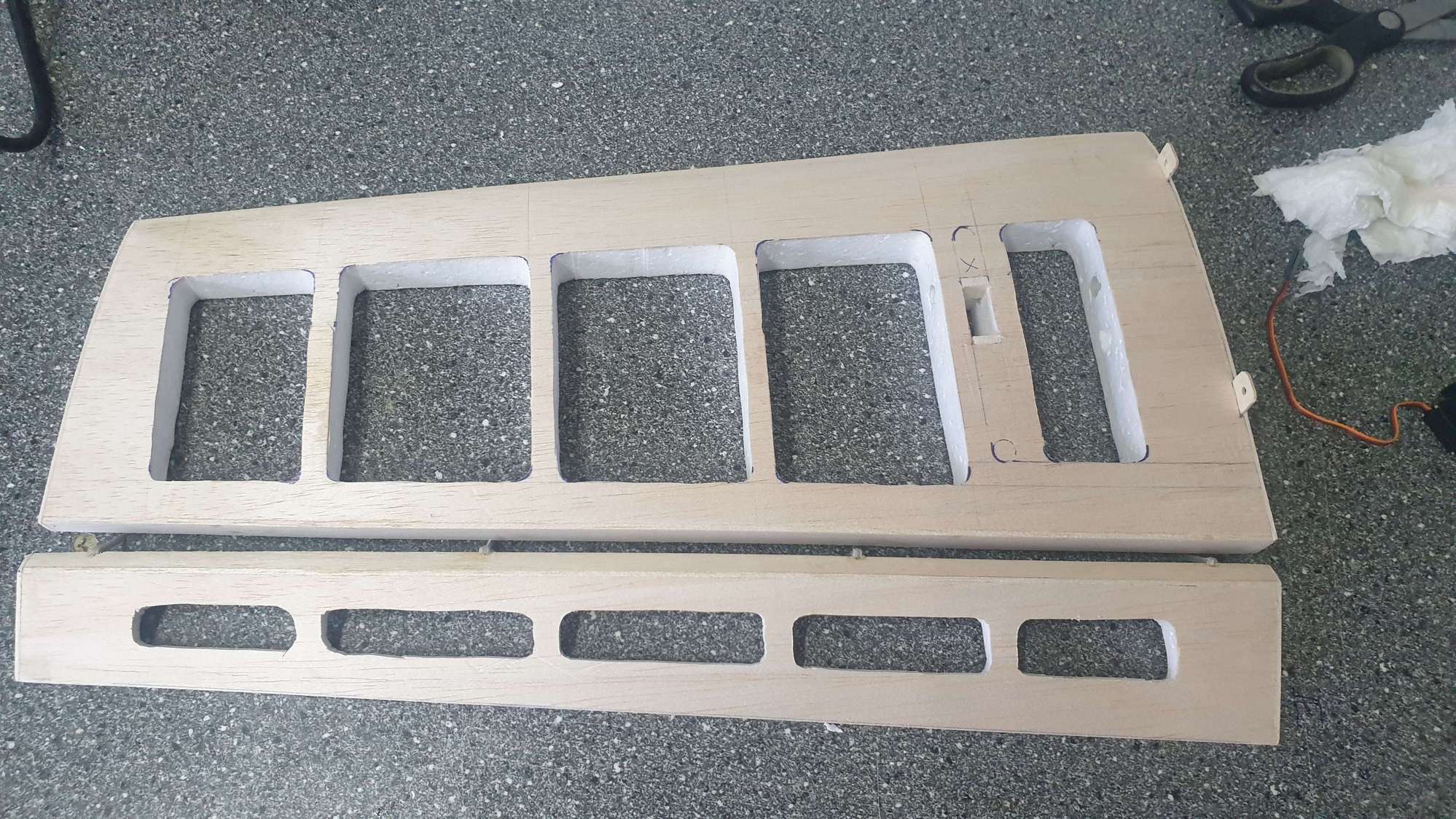
I have a small home shop with hot wire cutter, vacuum bag where I build planes my own - nothing high tech, so I build small fun planes up to 1200mm wingspan I used to make wings out of foam core and blasa sheeted.
Anyway they were always little havier than balsa build up wings.
My last plane is 1040mm wing span and tried lightening, cutting out space and living 1/2 inch ribs and contours.
The plane is small so I added no spars inside and the sheeting is 1mm thick.
After lightening I cover it with solar film (I'll provide picture later) and the weight of one panel covered ended up ~65g so 130g / full span wing.
The way I do is:
- cut the wings carefully. Result is there are no big gaps or waves. Sanding is very light.
- Prepare wing joint tube ( usually made of 2-3 layers of 48g FG and wetted with waterbased varnish - it-s strong enough and very light after cures)
- Prepare well selected balsa sheets (light), put them them together with blue tape
- Apply carefull light layer of PU glue both sides balsa and foam core. Really carefull with the glue quantities. I use light and struggle to see, make sure is wet everywhere then spray little water.
- Put the sandwich together carefully
- In the vaccum bag for 2-3 hours
- Cut out foam between ribs ( 10-15mm) and other reqired contours for servo or other required
- Cover the wing with Solar film
My question is how other people do their foam core wing for small plane, are there other building techniques using foam core for light wings?
What can I improve to get even lighter wings?
Thanks,
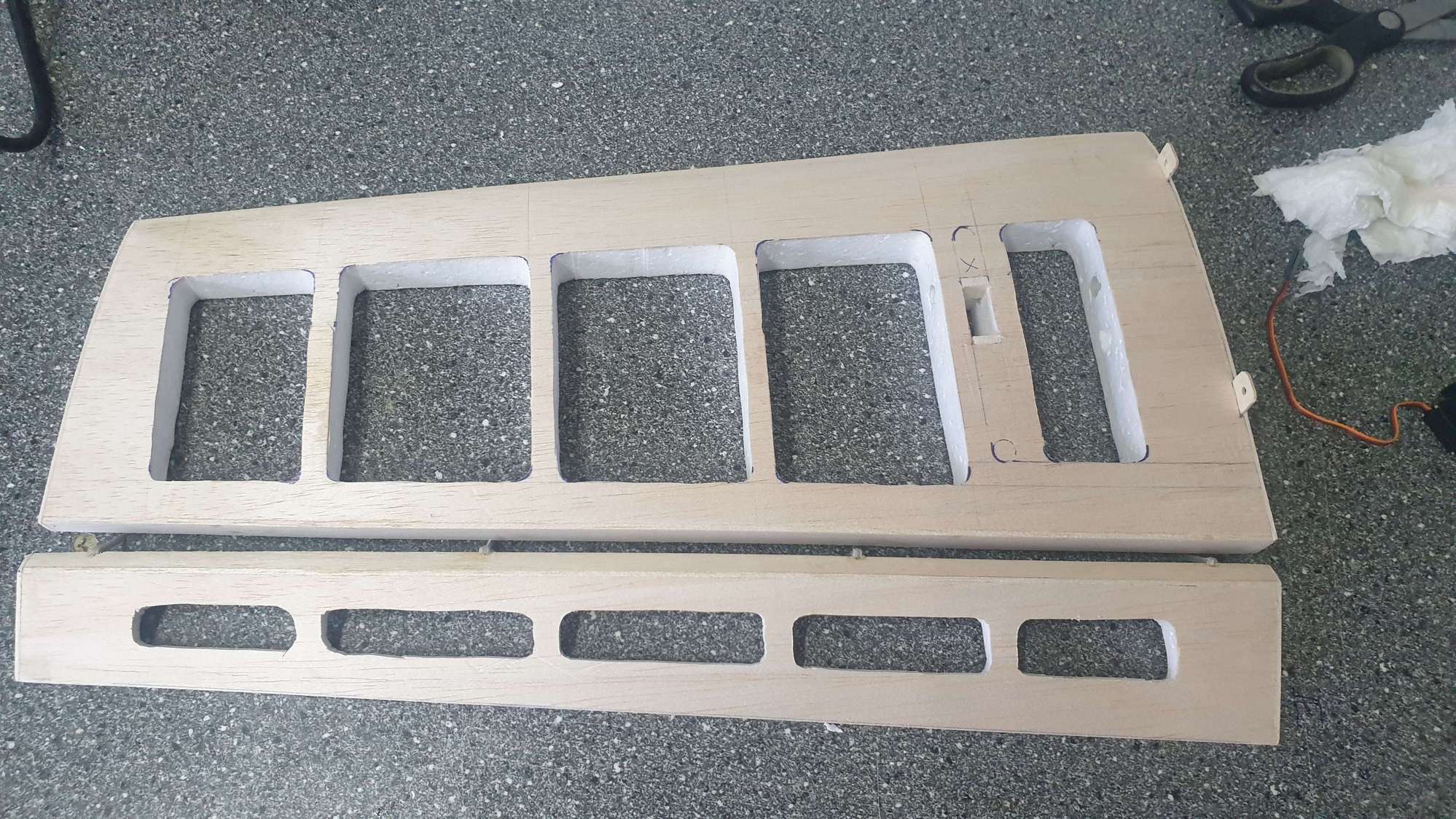
Last edited by critx; 06-30-2022 at 01:01 PM.
#4
Junior Member
Join Date: Feb 2023
Posts: 5
Likes: 0
Received 0 Likes
on
0 Posts

Hi,
On my old account (critx) I'm banned by the admins and the reason is that I'm a scammer. I suspect I had some kind of virus, but anyways it looks that I cannot get back that account anymore.
@Sensei it can be seen the cutouts in the cores on the plane you show in the pictures have been made by CNC. It looks very good.
I've build one profile plane for testing of the techinque and it came out very well ( I'm not alowed to add pictures until more than 10 posts ).
I like using foam core sheeted wings because I have the tools and vacuum system and I can build accurate and quick.
By removing some of the core the overall weight become much better.
Regards,
On my old account (critx) I'm banned by the admins and the reason is that I'm a scammer. I suspect I had some kind of virus, but anyways it looks that I cannot get back that account anymore.
@Sensei it can be seen the cutouts in the cores on the plane you show in the pictures have been made by CNC. It looks very good.
I've build one profile plane for testing of the techinque and it came out very well ( I'm not alowed to add pictures until more than 10 posts ).
I like using foam core sheeted wings because I have the tools and vacuum system and I can build accurate and quick.
By removing some of the core the overall weight become much better.
Regards,
#5


I used to do this, until I weighed the amount of foam removed vs the all up weight of the completely finished plane. Now I just worry about minimizing the type/amount of glue and wood (and all the other components). In my case, too much work for too little gain.
#6
Junior Member
Join Date: Feb 2023
Posts: 5
Likes: 0
Received 0 Likes
on
0 Posts

tedsander I see your point.
But in my case, I'm using the same technique like in the pictures posted by Sensei and I do this for small planes 50-55" wingspan, I am sheeting the wing with balsa under vacuum then I make the cutouts so it includes the balsa sheeting as well , after that I cover the whole wing with Solarfilm/Oracover. The cuts are 30-35% of the wing surface so that is the weight saved as well. The weight saved is not only foam weight.
Have a look at the fist post - and see how much area is empty... but that was a 40" plane
But in my case, I'm using the same technique like in the pictures posted by Sensei and I do this for small planes 50-55" wingspan, I am sheeting the wing with balsa under vacuum then I make the cutouts so it includes the balsa sheeting as well , after that I cover the whole wing with Solarfilm/Oracover. The cuts are 30-35% of the wing surface so that is the weight saved as well. The weight saved is not only foam weight.
Have a look at the fist post - and see how much area is empty... but that was a 40" plane
Last edited by dacair; 02-09-2023 at 10:55 AM.
#7


I get it, and more power too you for doing it! In my builds, I now leave the foam, and just essentially use cap strips periodically. Like the first pic in the thread, but imagine the foam itself all left in place. But, I'm getting a bit lazy in building, and now being officially "very old" the gain in performance edge is far overcome by my own decrease in performance..
#9
Junior Member
Join Date: Feb 2023
Posts: 5
Likes: 0
Received 0 Likes
on
0 Posts

Hi, I thought I don't start a new thread as my question is related to foam cores...
I always had an issue when I cutted foam cores with hotwire ( there's no CNC wire cutter in my area ). The issue is that the cores resulted thinner than the designed and the reason was known - it was because the wire is melting foam around it.
So question is, how thicker the template should be to compensate the additional foam melting.
I always had an issue when I cutted foam cores with hotwire ( there's no CNC wire cutter in my area ). The issue is that the cores resulted thinner than the designed and the reason was known - it was because the wire is melting foam around it.
So question is, how thicker the template should be to compensate the additional foam melting.
#10


There isn't a standard amount. It depends on the wire, the heat applied, and the speed used to cut. It may take a couple of tries with different templates to find the compensation that works best for your system.