Let's try to build a home made Kevlar fuel tank!
#1

Thread Starter

Hi friends,
I'm opening this new thread of mine to share my experiences, techniques, mistakes and suggestions with all fans of this hobby. What I want to talk to you about today is the creation of a kevlar tank for a turbine jet that I will soon set up: a 2.2mt "Predator" by PilotRc. Even if there are several videos on this topic on the net, my thread wants to be "down to earth", simple simple, made not by a professional but by a model maker who continues to have the passion to "try" and put himself to the test.
Let's start from the model: for this tank I was inspired by what PilotRc sells separately for its "Predator 2.2", a tank with integrated Uat (always full) of 4.6 Lt. The idea came to me because from a few months ago I bought a 3D printer and it is with this printer that I made the molds of the tank. The problem was finding the drawings of this tank and then converting them into 3D but luckily some users of a forum specialized in 3D printing and drawing (https://www.stampa3d-forum.it/) helped me. A forge of ideas and people who are not only capable but above all available. I posted the 2D Cad format photos of this tank and in a few days and several tweaks and modifications the "Stl" format of my tank and Uat is ready.
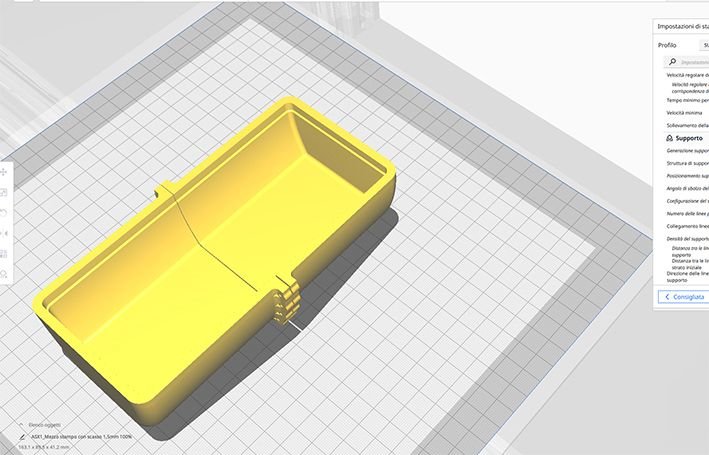

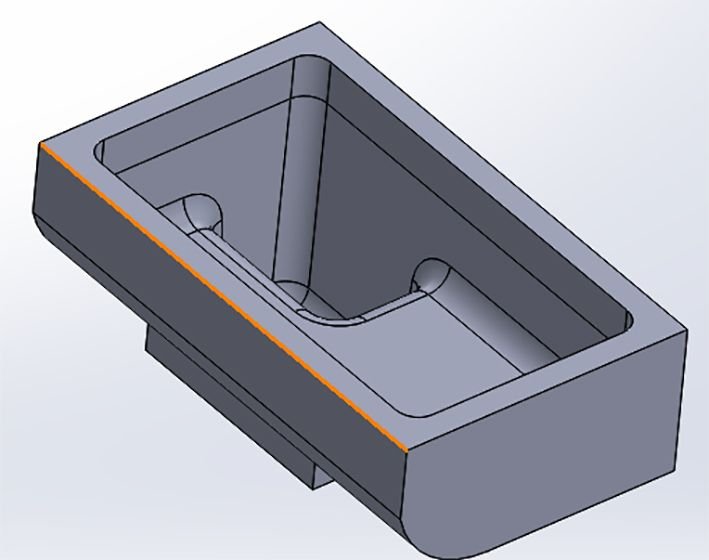
I'm opening this new thread of mine to share my experiences, techniques, mistakes and suggestions with all fans of this hobby. What I want to talk to you about today is the creation of a kevlar tank for a turbine jet that I will soon set up: a 2.2mt "Predator" by PilotRc. Even if there are several videos on this topic on the net, my thread wants to be "down to earth", simple simple, made not by a professional but by a model maker who continues to have the passion to "try" and put himself to the test.
Let's start from the model: for this tank I was inspired by what PilotRc sells separately for its "Predator 2.2", a tank with integrated Uat (always full) of 4.6 Lt. The idea came to me because from a few months ago I bought a 3D printer and it is with this printer that I made the molds of the tank. The problem was finding the drawings of this tank and then converting them into 3D but luckily some users of a forum specialized in 3D printing and drawing (https://www.stampa3d-forum.it/) helped me. A forge of ideas and people who are not only capable but above all available. I posted the 2D Cad format photos of this tank and in a few days and several tweaks and modifications the "Stl" format of my tank and Uat is ready.
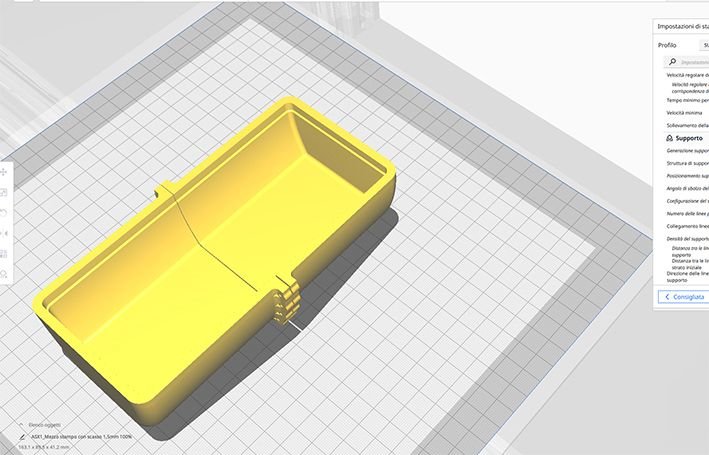

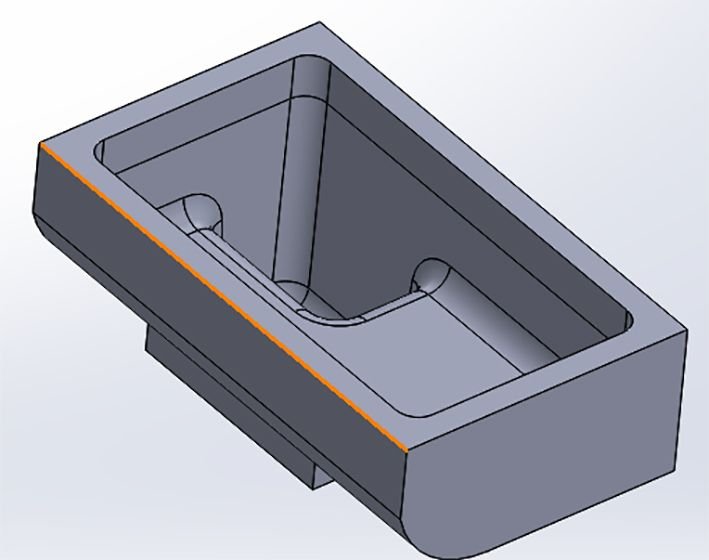
#2

Thread Starter

Slightly reduced to have a capacity of about 3.5 liters (more than enough for my 120N turbine) the main part of the tank has been designed in 4 shells (two halves for the lower part (which also has a flare where the upper to close the two shells with a perfect joint) and two halves for the upper one to allow the shot to be easily extracted from the master.
Once the files were obtained, I started to do some printing tests on my Artillery Sidewinder X2 to find (I use “Cura” as the slicer) the right parameters that would allow for the smoothest internal mold surface possible. Once I found the optimal configuration I started printing the molds. It took about 55 hours of printing to get all the pieces and at this point I dedicated myself to the finishing work.
(continued)
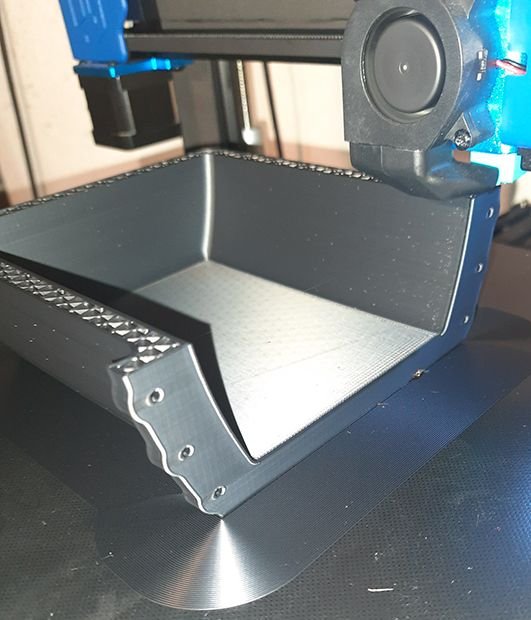
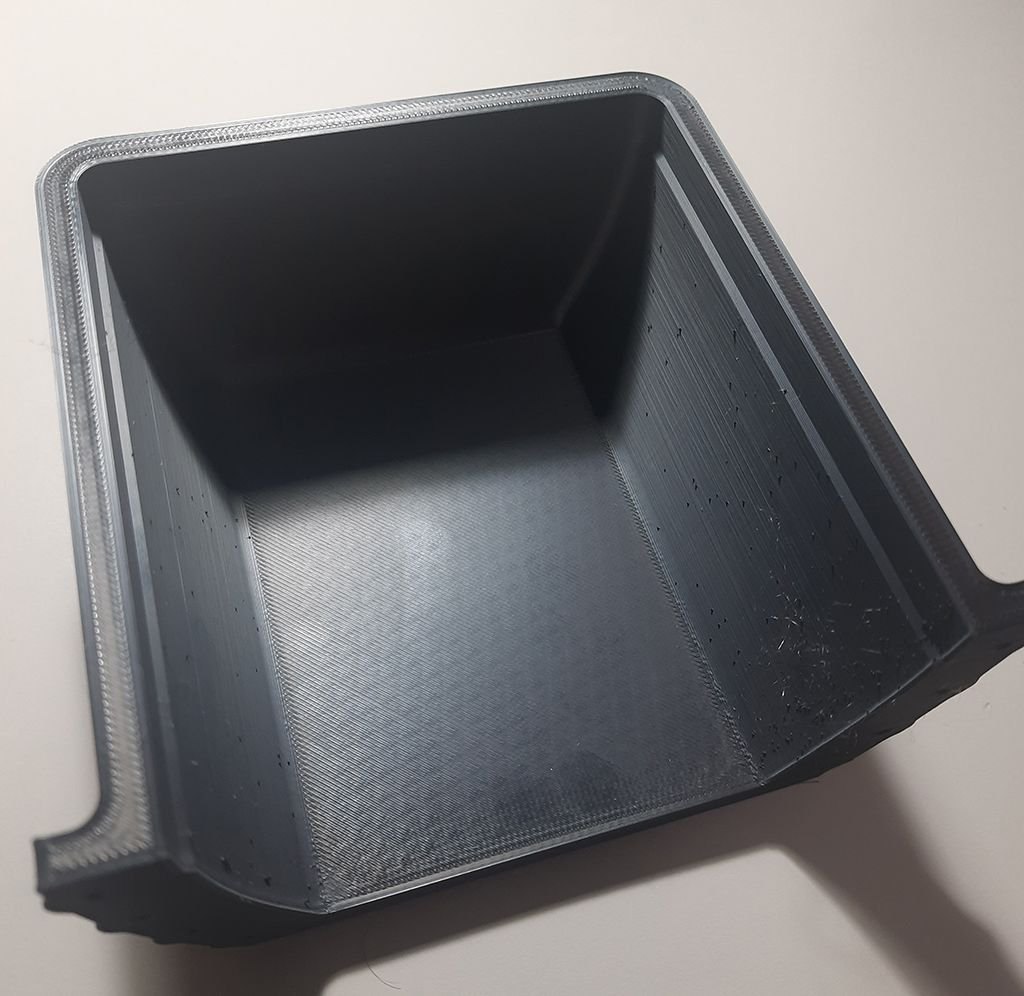
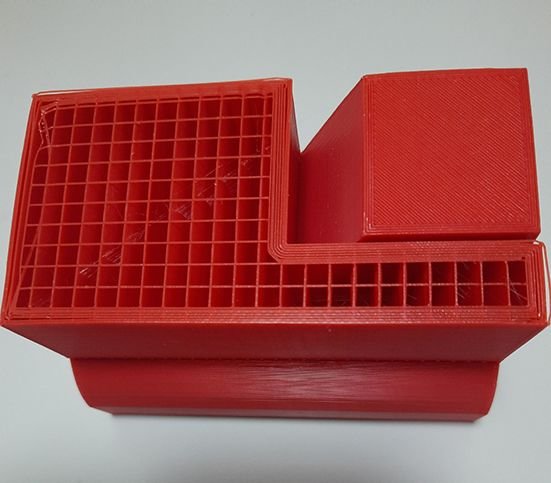
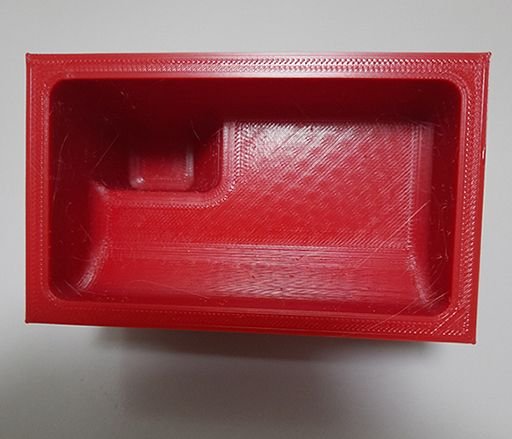
Once the files were obtained, I started to do some printing tests on my Artillery Sidewinder X2 to find (I use “Cura” as the slicer) the right parameters that would allow for the smoothest internal mold surface possible. Once I found the optimal configuration I started printing the molds. It took about 55 hours of printing to get all the pieces and at this point I dedicated myself to the finishing work.
(continued)
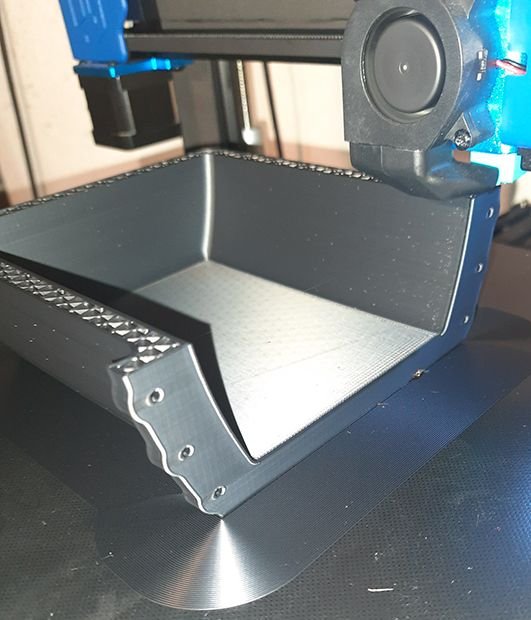
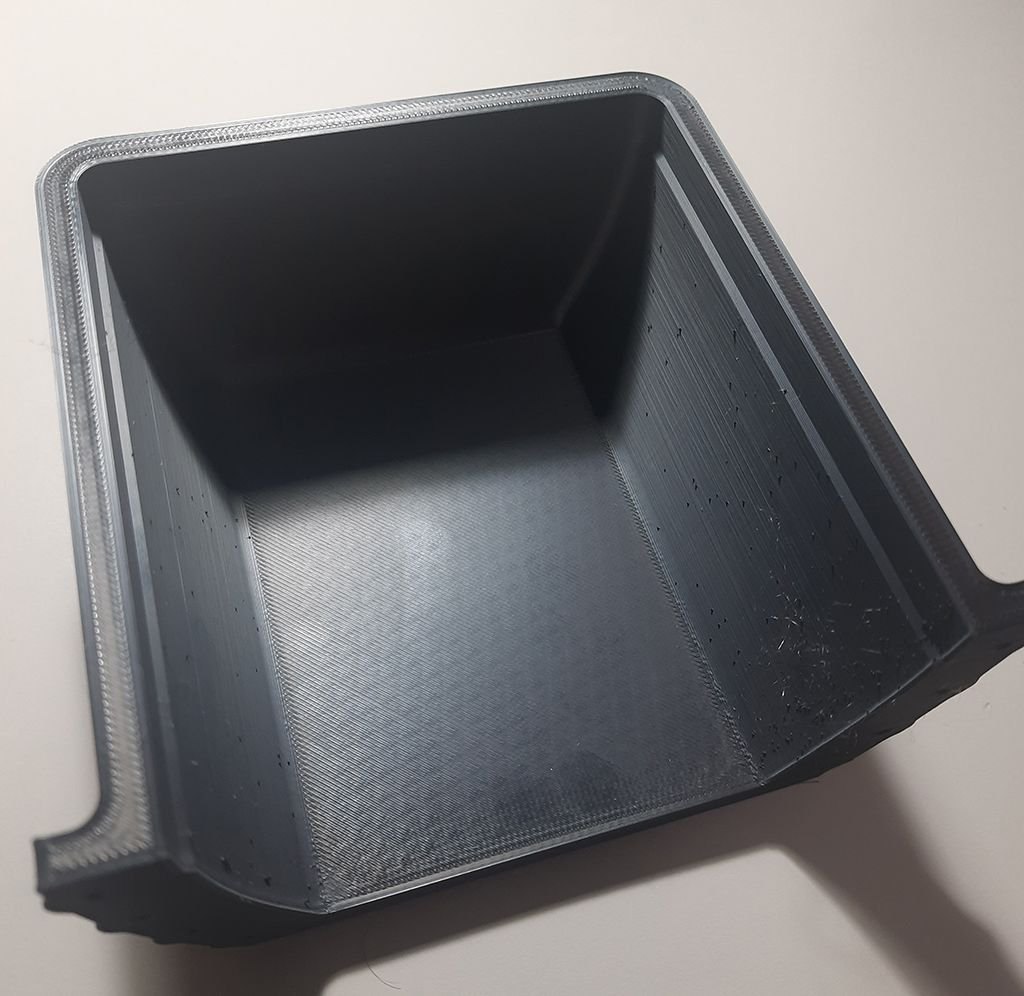
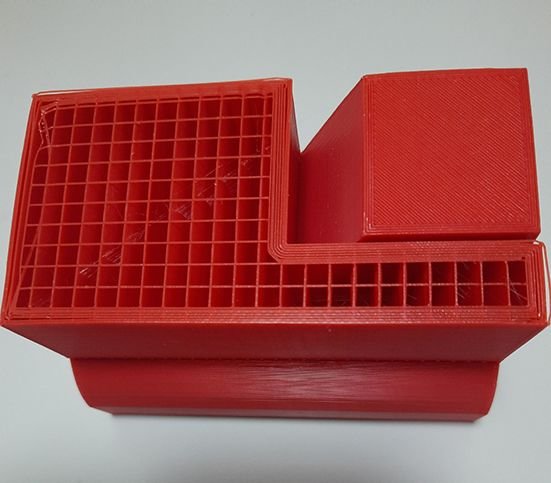
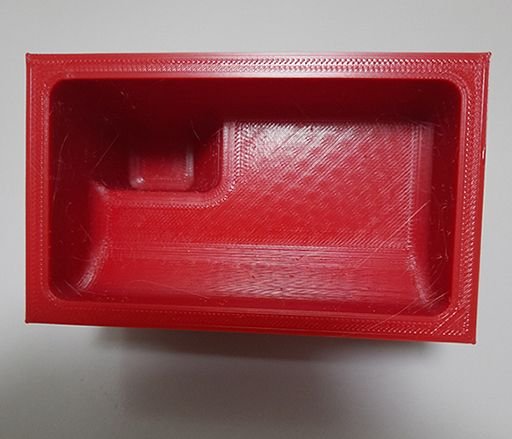
#3

Thread Starter

Hello, lt's Go on.
The pieces printed with the 3D printer, however precise and of quality they are, have small jaggies which, if not corrected, would leave fingerprints on the printed piece. So I sanded the interior first with 120 sandpaper, then 200 and finally 360. I then gave a nice coat of catalyzed spray filler and then a varnish with 2K acrylic paint. The result was mirror surfaces!
Those who are somewhat familiar with composite molds know that every new mold must be treated with a release agent before molding. So you need to get a release wax for molds (you can find it in all online shops of modeling or composite processing items (I use Sorvolando Compositi "sorvolandocompositi.it" cost about 25 euros for a 400/500 gram jar which will lasts a lifetime and, which creates added value, a person who knows how to give you lots of useful advice). This wax must be applied inside the mold with a soft cotton cloth with circular movements being careful to treat all points of the mold and the upper part where the fabric and the resin will overflow). 7/8 coats of wax (each coat interspersed with air drying for about twenty minutes and light polishing) for a new mold are sufficient. In subsequent pressings he was able to give only a couple of coats of wax. After the wax, I also use polyvinyl alcohol given with a spray gun / airbrush: it is an additional release agent that forms a water-soluble film and which helps the extraction of the molded piece (someone does not use it).
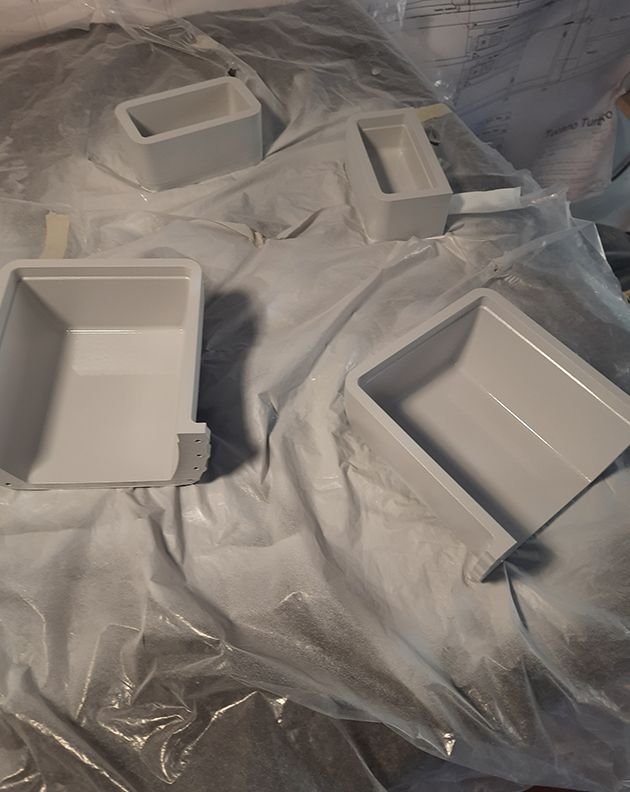
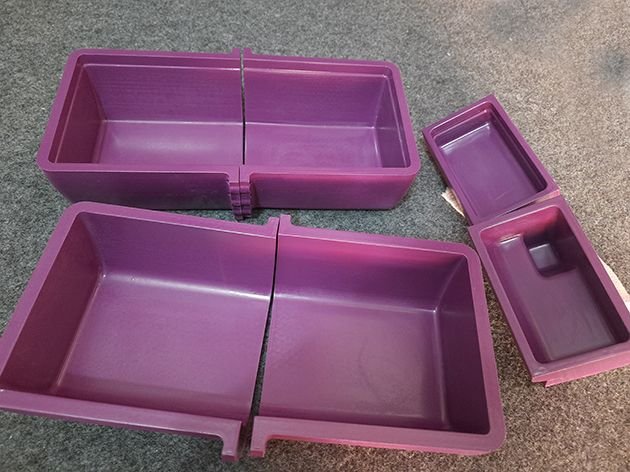
The pieces printed with the 3D printer, however precise and of quality they are, have small jaggies which, if not corrected, would leave fingerprints on the printed piece. So I sanded the interior first with 120 sandpaper, then 200 and finally 360. I then gave a nice coat of catalyzed spray filler and then a varnish with 2K acrylic paint. The result was mirror surfaces!
Those who are somewhat familiar with composite molds know that every new mold must be treated with a release agent before molding. So you need to get a release wax for molds (you can find it in all online shops of modeling or composite processing items (I use Sorvolando Compositi "sorvolandocompositi.it" cost about 25 euros for a 400/500 gram jar which will lasts a lifetime and, which creates added value, a person who knows how to give you lots of useful advice). This wax must be applied inside the mold with a soft cotton cloth with circular movements being careful to treat all points of the mold and the upper part where the fabric and the resin will overflow). 7/8 coats of wax (each coat interspersed with air drying for about twenty minutes and light polishing) for a new mold are sufficient. In subsequent pressings he was able to give only a couple of coats of wax. After the wax, I also use polyvinyl alcohol given with a spray gun / airbrush: it is an additional release agent that forms a water-soluble film and which helps the extraction of the molded piece (someone does not use it).
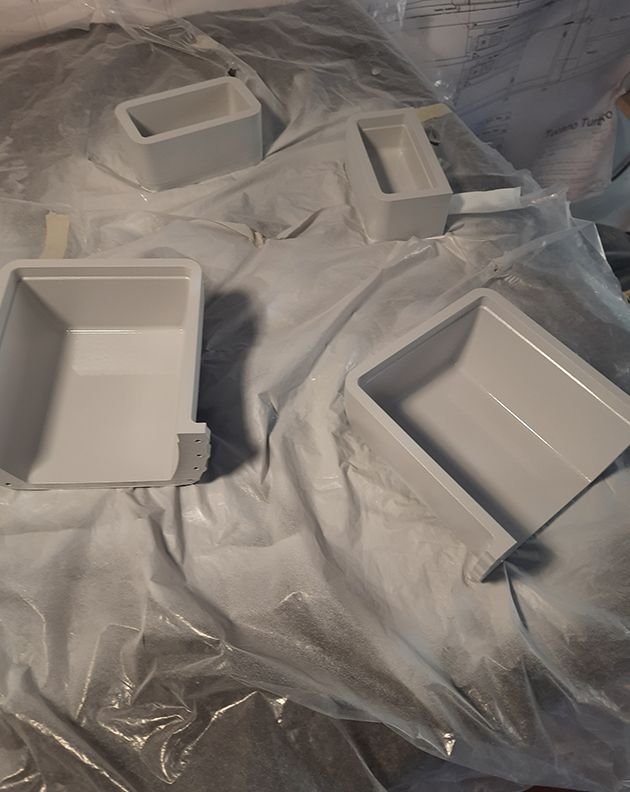
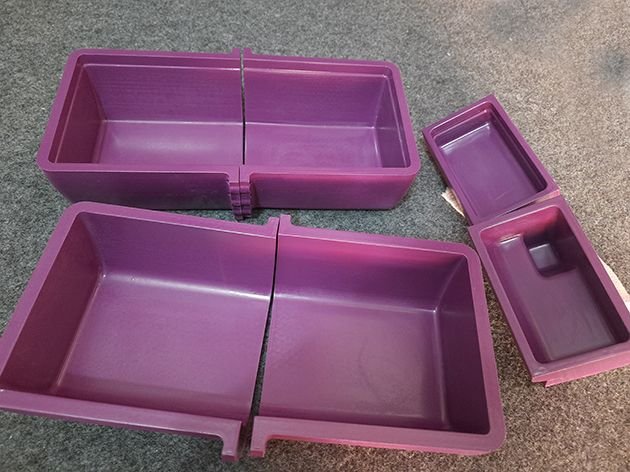
#4

Thread Starter

We continue...
At this point you will be ready to start preparing the resin and fabric for the tank lamination. For the fabric I decided to use a first layer of 170gmq Kevlar and two layers of 160gmq glass fabric. The choice proved to be right as I got a light and resistant tank. And here, however, the first problem arose that I hadn't considered: when I went to cut the Kevlar I found myself with scissors and an electric cutter that I normally use which are unusable. I tried with different types of scissors but without being able to cut the kevlar. I started looking for an effective system and I discovered that special scissors are needed for this type of aramid fabric (as well as carbon in part). By pure chance, I found on the web a company with 100% certified Italian products that only produces scissors (it's called "Millemetri" - https://millemetri.it). It offers a wide range of scissors but what interested me was the specific "Technik" line for industrial use in cutting composite fibers such as Kevlar, glass fiber and carbon fiber. I contacted them and they recommended the “Art. 329 - Tailor 9.5 Aramid” 24cm (9.5 inches) long. Tailor shears, size 9.5" (24.5 cm) with blades and screws in special 62 HRC steel with micro-toothing (on one or both blades of your choice) ideal for cutting aramid fibers - Kevlar, glass fiber, fiber of carbon. I ordered them and… show! Perfect, precise cut, without filleting of the fabric, a pleasure ... But be careful because the company has recommended itself (as I later discovered it is also reported on the site) that maintenance is of fundamental importance for these scissors (and for all of them in general) : simple tricks that can avoid annoying long-term problems. After use, it is recommended to avoid leaving residues of any kind on the blade, including water or dirt in general; periodically clean the blades by opening the scissors and oiling them in the sliding points between the blades with lubricating oil (pharmaceutical grade vaseline oil is excellent). I am also attaching a short video (forgive the quality...)
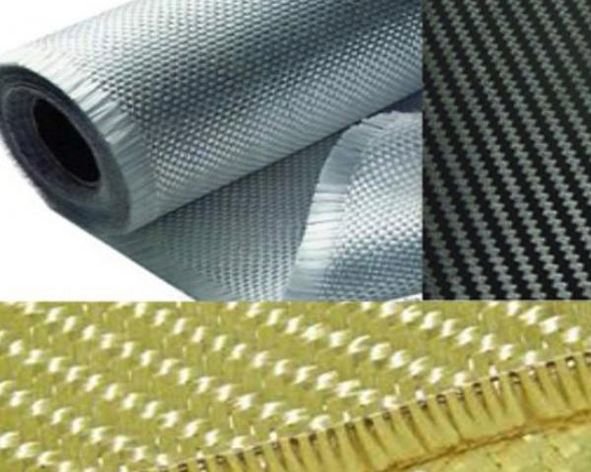
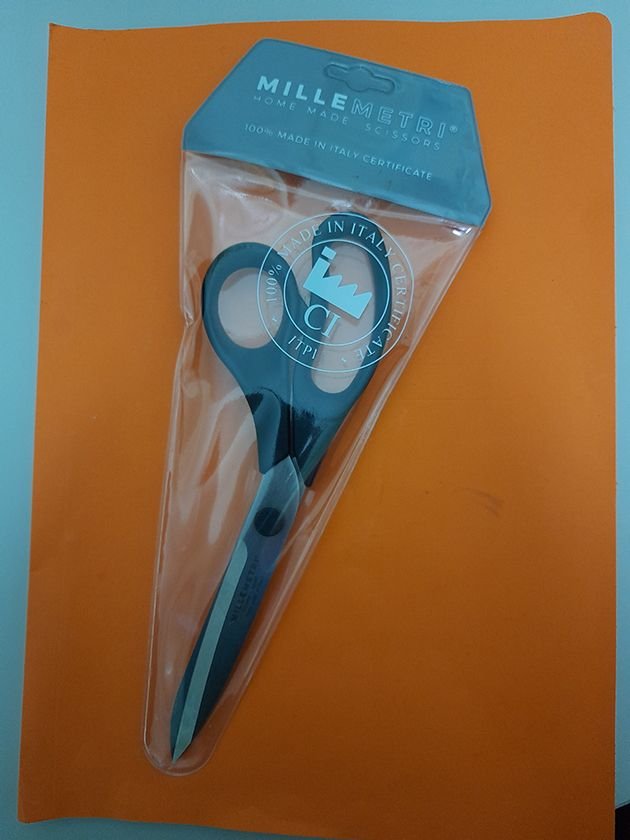
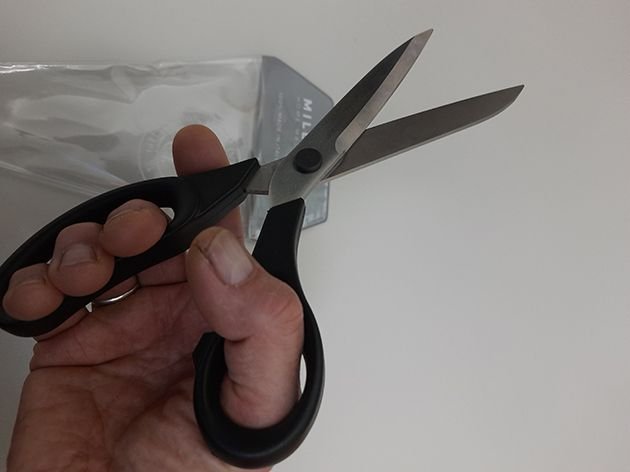
At this point you will be ready to start preparing the resin and fabric for the tank lamination. For the fabric I decided to use a first layer of 170gmq Kevlar and two layers of 160gmq glass fabric. The choice proved to be right as I got a light and resistant tank. And here, however, the first problem arose that I hadn't considered: when I went to cut the Kevlar I found myself with scissors and an electric cutter that I normally use which are unusable. I tried with different types of scissors but without being able to cut the kevlar. I started looking for an effective system and I discovered that special scissors are needed for this type of aramid fabric (as well as carbon in part). By pure chance, I found on the web a company with 100% certified Italian products that only produces scissors (it's called "Millemetri" - https://millemetri.it). It offers a wide range of scissors but what interested me was the specific "Technik" line for industrial use in cutting composite fibers such as Kevlar, glass fiber and carbon fiber. I contacted them and they recommended the “Art. 329 - Tailor 9.5 Aramid” 24cm (9.5 inches) long. Tailor shears, size 9.5" (24.5 cm) with blades and screws in special 62 HRC steel with micro-toothing (on one or both blades of your choice) ideal for cutting aramid fibers - Kevlar, glass fiber, fiber of carbon. I ordered them and… show! Perfect, precise cut, without filleting of the fabric, a pleasure ... But be careful because the company has recommended itself (as I later discovered it is also reported on the site) that maintenance is of fundamental importance for these scissors (and for all of them in general) : simple tricks that can avoid annoying long-term problems. After use, it is recommended to avoid leaving residues of any kind on the blade, including water or dirt in general; periodically clean the blades by opening the scissors and oiling them in the sliding points between the blades with lubricating oil (pharmaceutical grade vaseline oil is excellent). I am also attaching a short video (forgive the quality...)
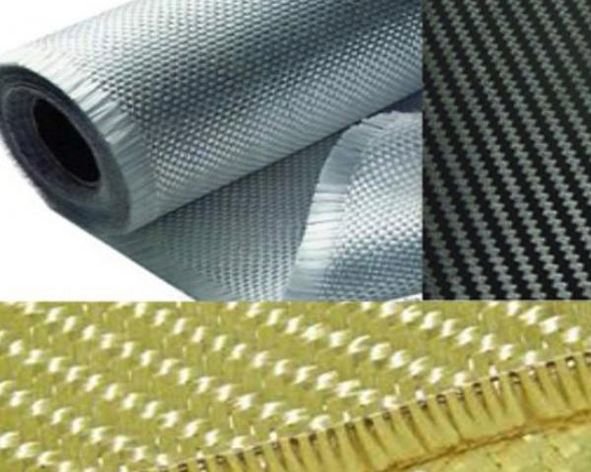
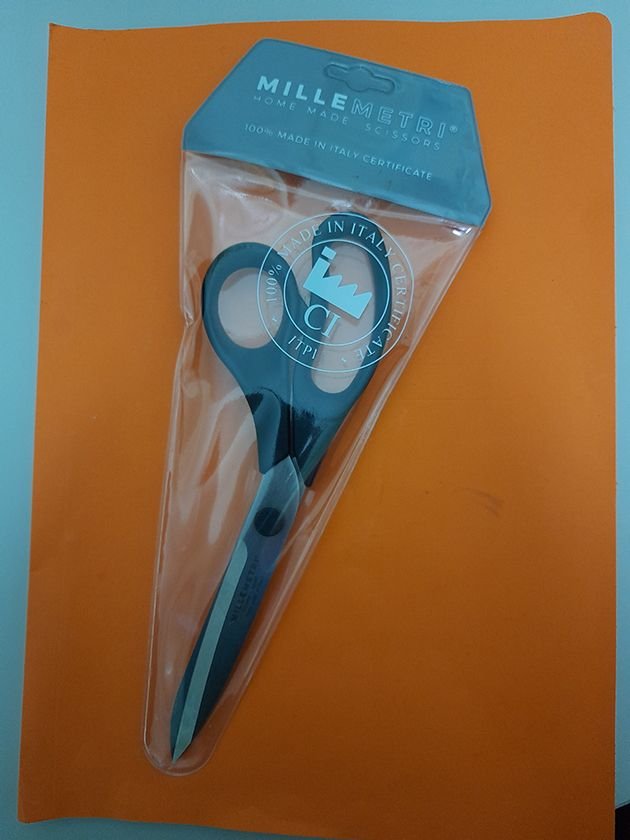
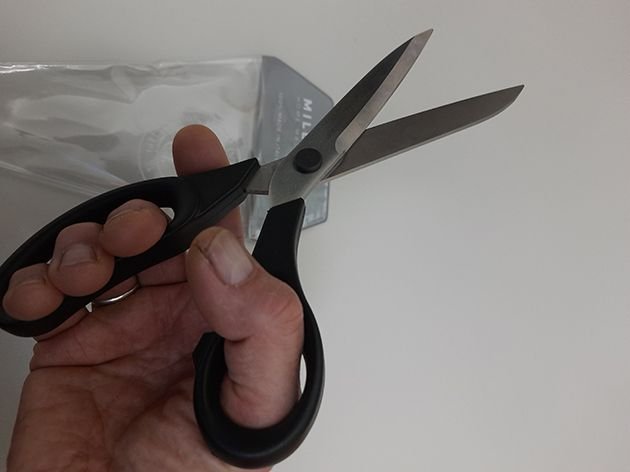
#5

Thread Starter

Let us conclude the brief summary.
We had remained at the cutting of the fabrics, solved the problem before starting the lamination (spreading of the fabric and then of the resin) you will have to prepare pieces of kevlar and glass fabric that best adapt to the mold and that cover it all overhanging a a little (you will trim the excess once all the fabric has been placed on the mould). I leave the choice of epoxy resin to you (never use polyester because it shrinks and stinks to death) but I recommend specialized shops (cost of 1kg of resin + catalyst from 20 to 30 euros depending on the brand). For this tank I used about 160 grams of which 10/15% is lost with excess fabric.
The lamination work starts now (try to work in an environment with a temperature not lower than 18 degrees otherwise the catalyst will be slowed down): mix the resin and the catalyst with a precision scale (once the resin has been mixed I usually pour it from paper cup in a plastic saucer to prevent it from catalyzing sooner than expected (too much resin in a small container has a faster chemical reaction); once this is done, start spreading the resin inside the mold with a soft brush; take the first piece of Kevlar that you have cut and arrange it with your hands inside the mold making it adhere well with your fingers to the walls (use latex gloves!!), then with the brush lightly soaked in resin dab on the fabric impregnating it well (you will notice where it is impregnated and where not by the change of color which will become dark where it has absorbed the resin.After this, go on to spread the second layer with the piece of glass fabric and with the same procedure make it adhere to the mold and impregnate it well. Once this is done, the work is almost completed for the third layer as well. To make the inside of the tank as smooth and uniform as possible you will need to use a piece of Peelply fabric which is a synthetic fabric which has the particularity of not sticking permanently to the resin but can be removed once the piece has dried, taking away the resin in excess and making the surfaces uniform (cost a few euros per 1m2). You spread it like the previous layers in the mold without however sprinkling it with resin: you lay it down with your hands and with a brush without resin you make it adhere well.
Now you have two options: either leave the mold as it is making sure that all the fabric adheres well to the walls of the mold to avoid bubbles, or get yourself a vacuum device and put all the pieces inside a special nylon bag and let the vacuum press all the fabric against the mold reproducing exactly its surface. But here a separate chapter opens that we will see in another article.
Laminated everything we let it catalyze for 12/24 hours depending on the ambient temperature and then we remove the pieces from the moulds. If the wax and the polyvinyl have been given well, you won't have much difficulty getting the piece out. A little more complicated to get it out of the Uat mold which has a deeper part. Help yourself with a plastic spatula and slowly detach the walls first and then the whole piece should come out.
Done! now you have the two shells of the tanks which, once trimmed, you will join and glue with epoxy glue. Once glued, for safety, a small strip of Kevlar is glued over the joint to reinforce the coupling point of the two shells. Finally choose the petrol (or kerosene) feed connectors and always glue them with epoxy. I recommend gluing all the power lines except the main front ones (tank and Uat) before joining the two shells, you work better from the inside. Before mounting it on the model, I recommend you do a leak test in a basin of water by putting it under pressure by blowing into it. You never know!
I hope I have been clear enough. My tank came out quite well, not perfect, but being the first tank I'm happy with it. You learn by making mistakes.

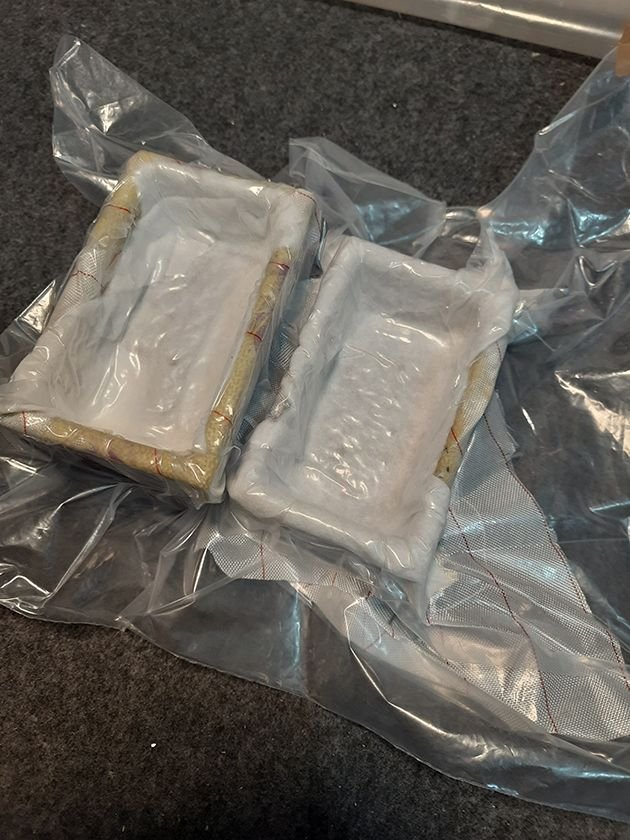
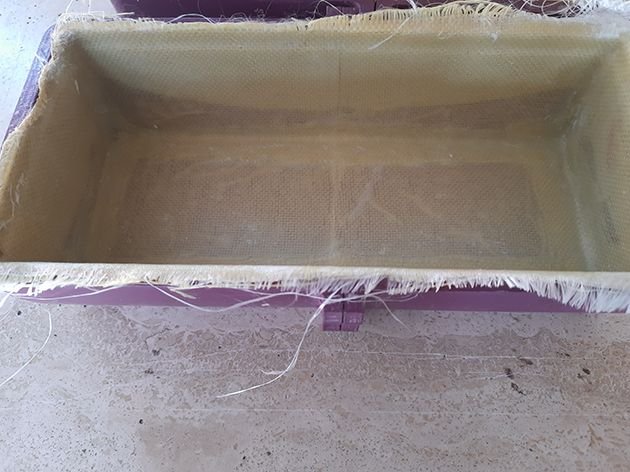
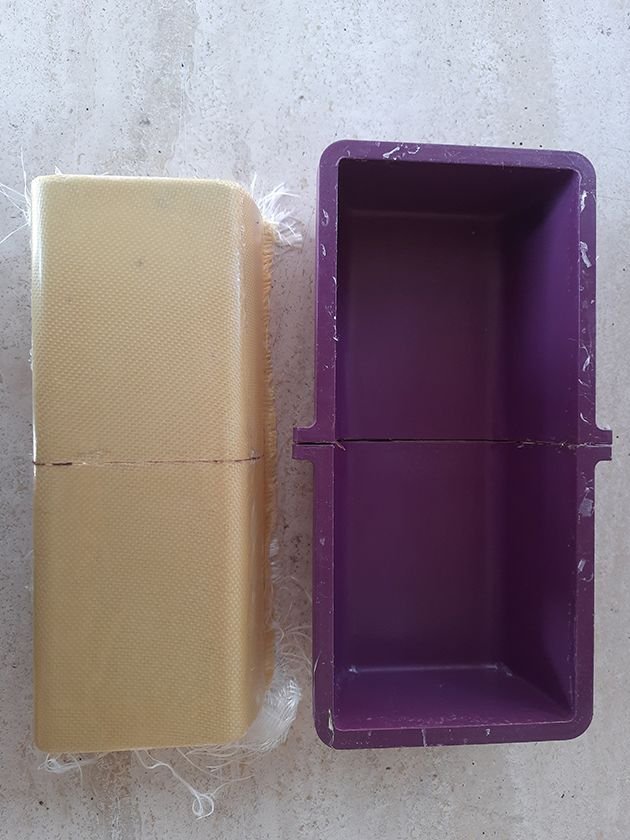
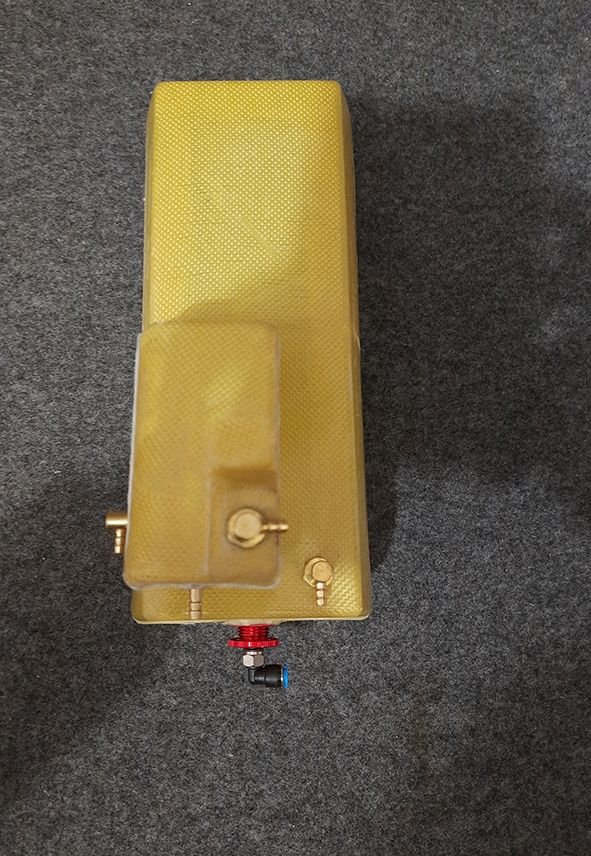
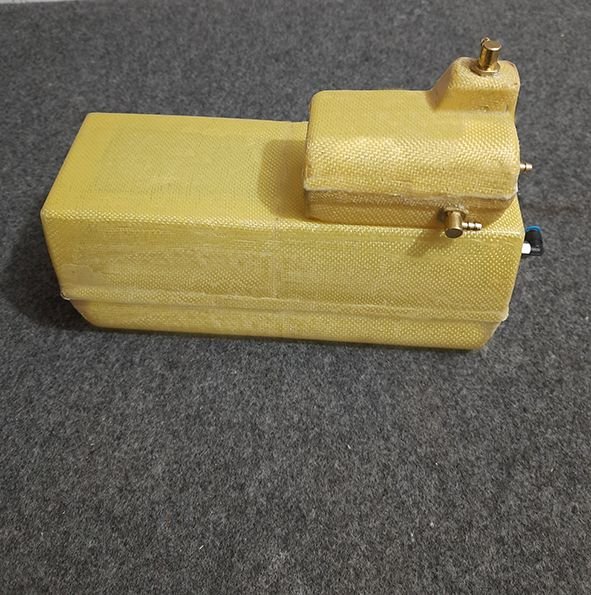
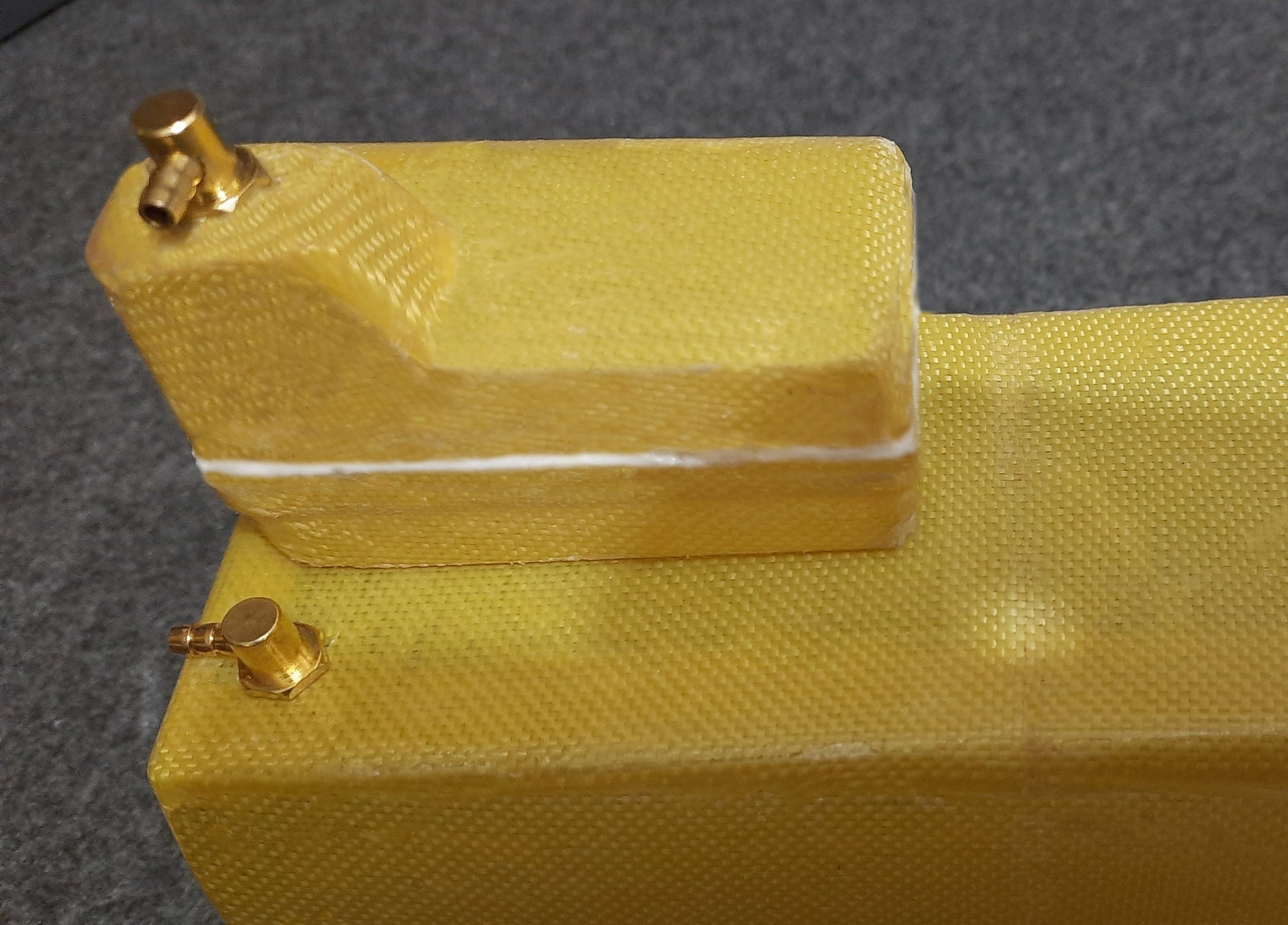
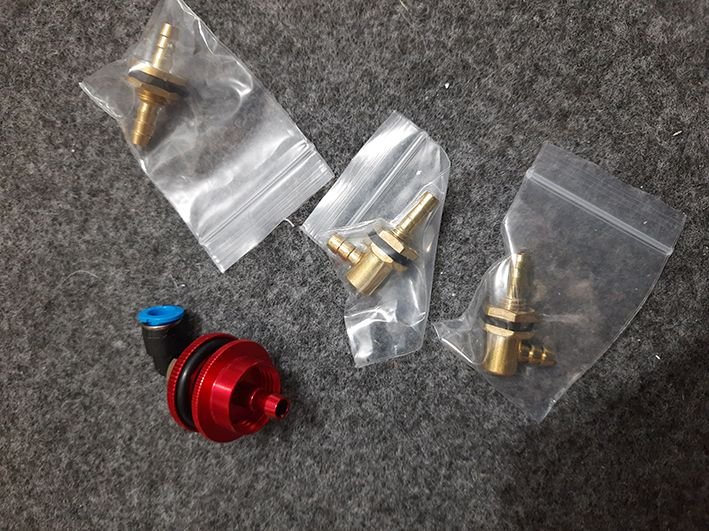
We had remained at the cutting of the fabrics, solved the problem before starting the lamination (spreading of the fabric and then of the resin) you will have to prepare pieces of kevlar and glass fabric that best adapt to the mold and that cover it all overhanging a a little (you will trim the excess once all the fabric has been placed on the mould). I leave the choice of epoxy resin to you (never use polyester because it shrinks and stinks to death) but I recommend specialized shops (cost of 1kg of resin + catalyst from 20 to 30 euros depending on the brand). For this tank I used about 160 grams of which 10/15% is lost with excess fabric.
The lamination work starts now (try to work in an environment with a temperature not lower than 18 degrees otherwise the catalyst will be slowed down): mix the resin and the catalyst with a precision scale (once the resin has been mixed I usually pour it from paper cup in a plastic saucer to prevent it from catalyzing sooner than expected (too much resin in a small container has a faster chemical reaction); once this is done, start spreading the resin inside the mold with a soft brush; take the first piece of Kevlar that you have cut and arrange it with your hands inside the mold making it adhere well with your fingers to the walls (use latex gloves!!), then with the brush lightly soaked in resin dab on the fabric impregnating it well (you will notice where it is impregnated and where not by the change of color which will become dark where it has absorbed the resin.After this, go on to spread the second layer with the piece of glass fabric and with the same procedure make it adhere to the mold and impregnate it well. Once this is done, the work is almost completed for the third layer as well. To make the inside of the tank as smooth and uniform as possible you will need to use a piece of Peelply fabric which is a synthetic fabric which has the particularity of not sticking permanently to the resin but can be removed once the piece has dried, taking away the resin in excess and making the surfaces uniform (cost a few euros per 1m2). You spread it like the previous layers in the mold without however sprinkling it with resin: you lay it down with your hands and with a brush without resin you make it adhere well.
Now you have two options: either leave the mold as it is making sure that all the fabric adheres well to the walls of the mold to avoid bubbles, or get yourself a vacuum device and put all the pieces inside a special nylon bag and let the vacuum press all the fabric against the mold reproducing exactly its surface. But here a separate chapter opens that we will see in another article.
Laminated everything we let it catalyze for 12/24 hours depending on the ambient temperature and then we remove the pieces from the moulds. If the wax and the polyvinyl have been given well, you won't have much difficulty getting the piece out. A little more complicated to get it out of the Uat mold which has a deeper part. Help yourself with a plastic spatula and slowly detach the walls first and then the whole piece should come out.
Done! now you have the two shells of the tanks which, once trimmed, you will join and glue with epoxy glue. Once glued, for safety, a small strip of Kevlar is glued over the joint to reinforce the coupling point of the two shells. Finally choose the petrol (or kerosene) feed connectors and always glue them with epoxy. I recommend gluing all the power lines except the main front ones (tank and Uat) before joining the two shells, you work better from the inside. Before mounting it on the model, I recommend you do a leak test in a basin of water by putting it under pressure by blowing into it. You never know!
I hope I have been clear enough. My tank came out quite well, not perfect, but being the first tank I'm happy with it. You learn by making mistakes.

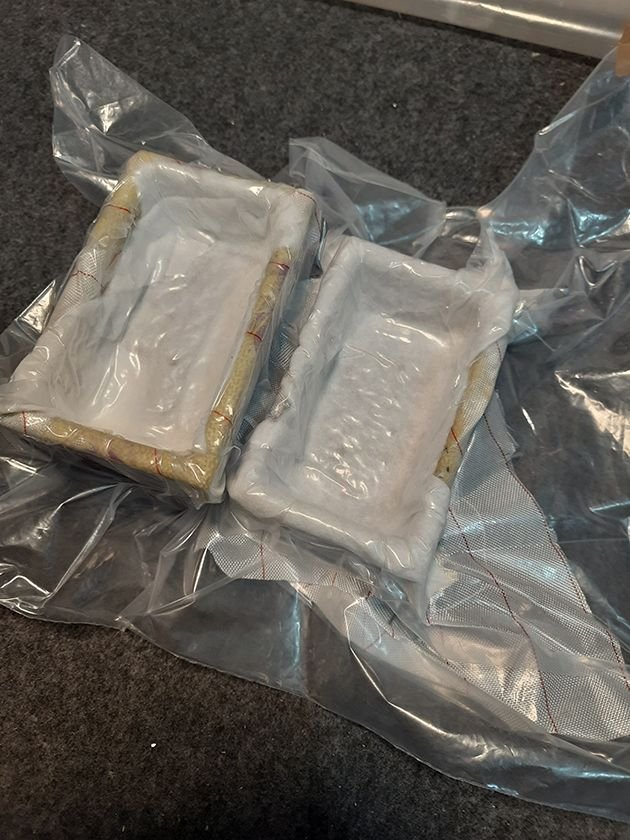
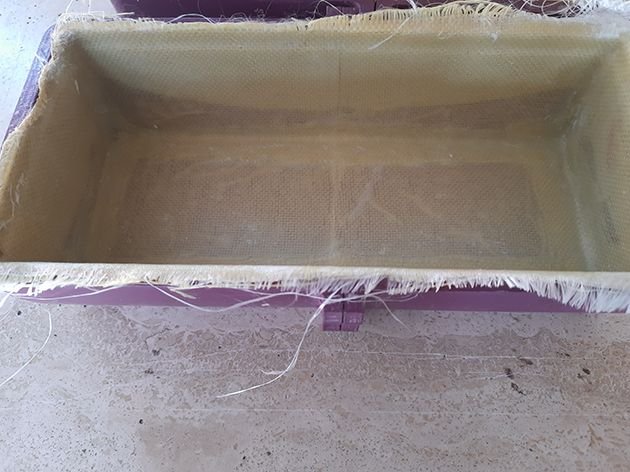
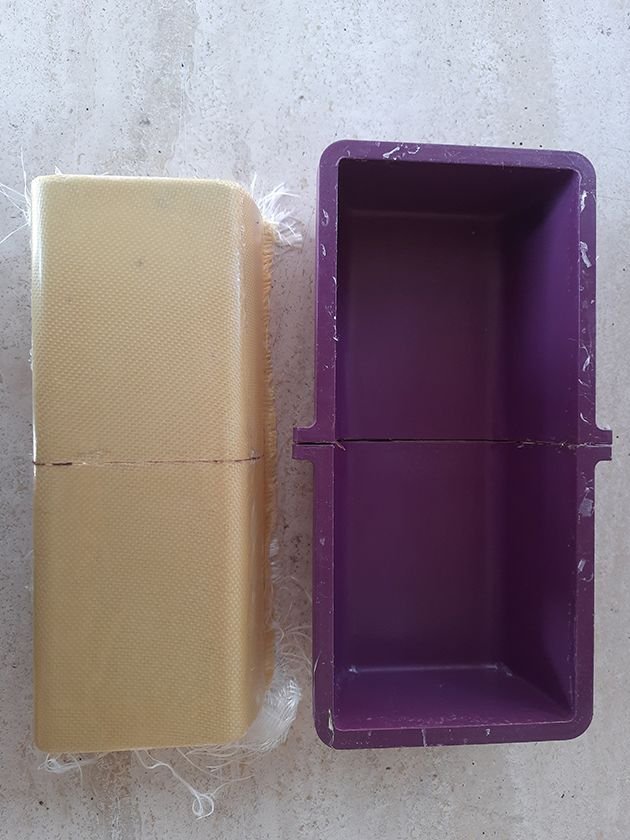
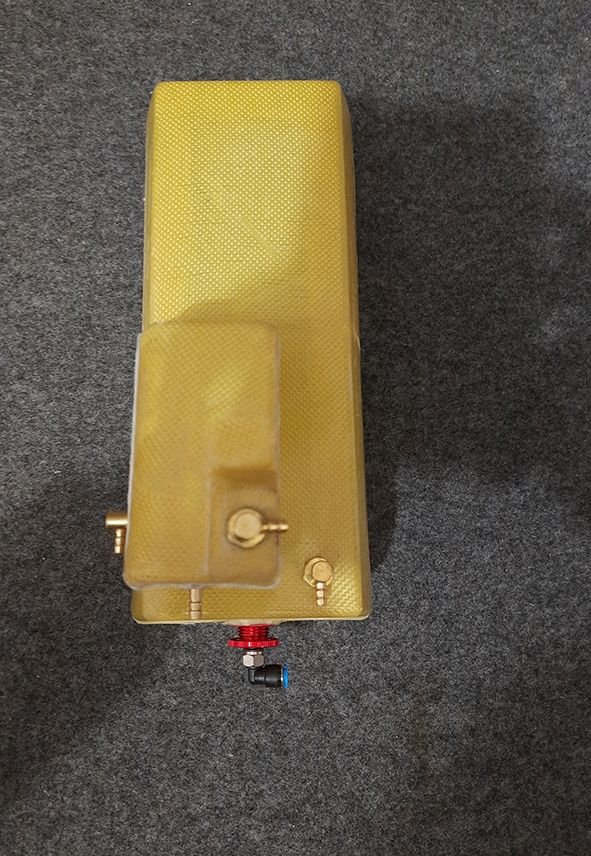
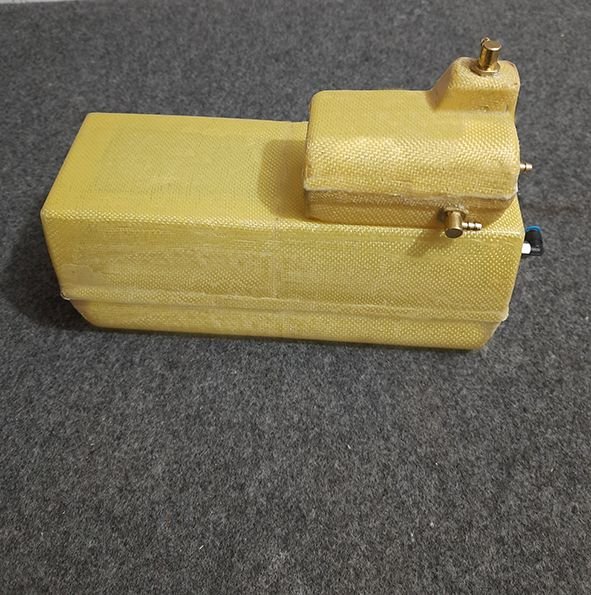
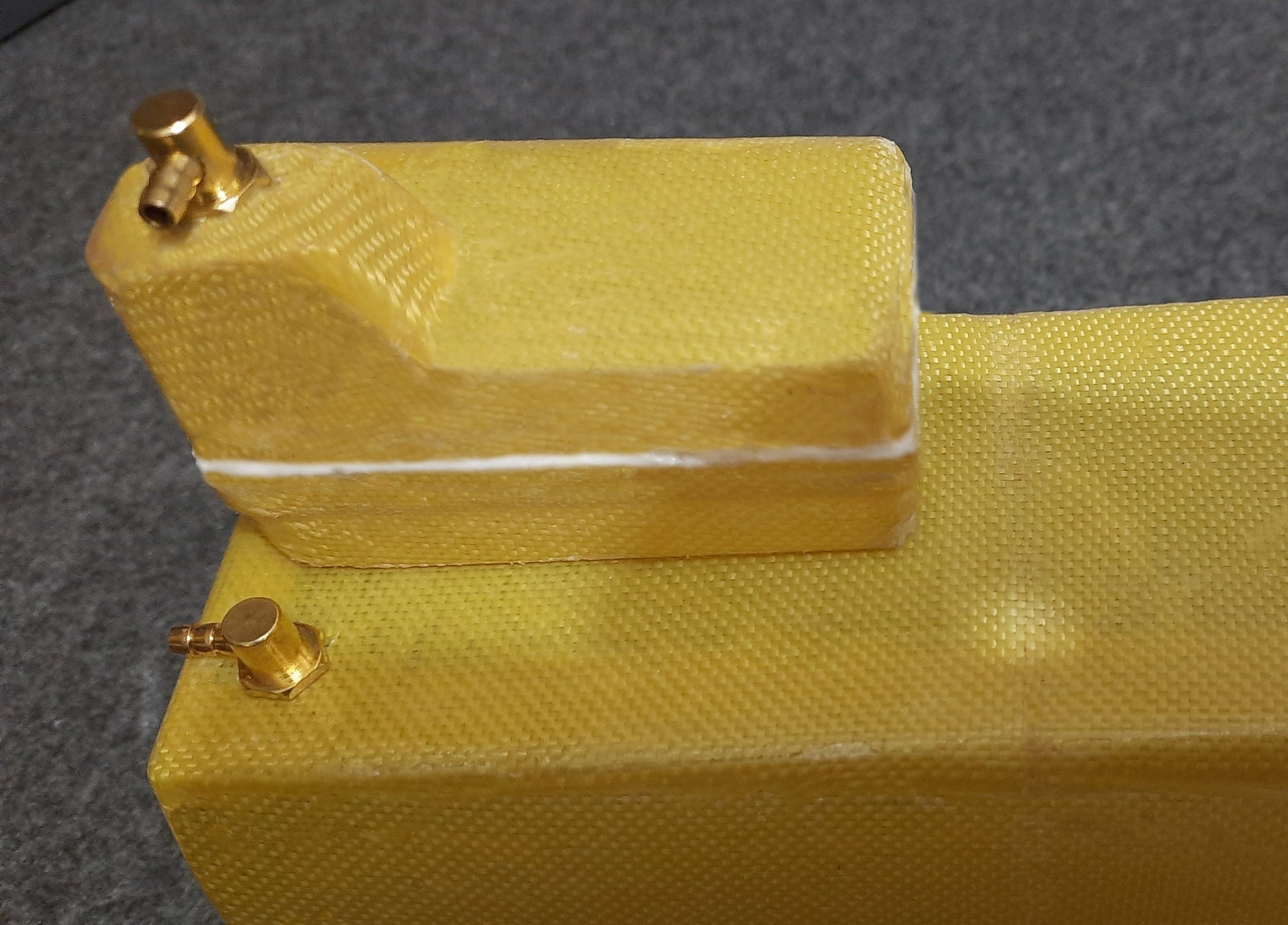
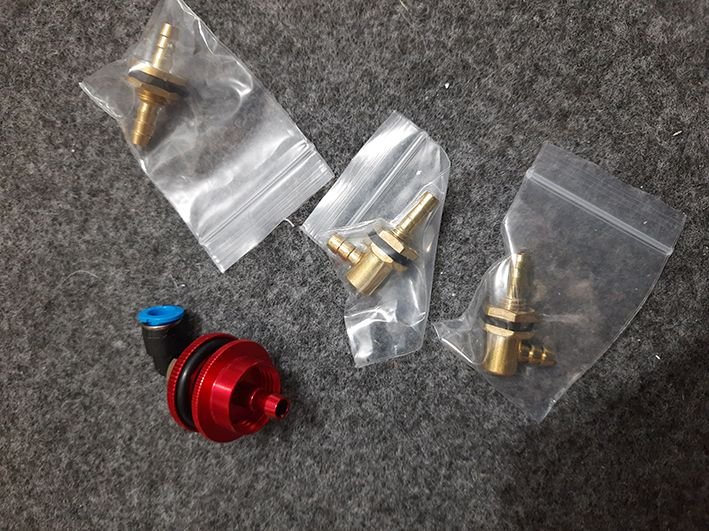
#6

Nice work,
I am always lazy to prepare the supposedly smooth finish, and just lay clear packaging tape.
Today I am trying PVA and I can see there will be imperfection finish imprinted on the surface already
Now with the painting the mold can you share a picture for the catalyzed filler? is it like two part filler like epoxy?
what is the final thickness need to be incorporated with the negative to achieve correct result?
I am always lazy to prepare the supposedly smooth finish, and just lay clear packaging tape.
Today I am trying PVA and I can see there will be imperfection finish imprinted on the surface already

Now with the painting the mold can you share a picture for the catalyzed filler? is it like two part filler like epoxy?
what is the final thickness need to be incorporated with the negative to achieve correct result?
#7

Thread Starter

The primer that I used is a two-component acrylic auto body primer. Two coats alternating with light sanding are sufficient. Then I used a two-component acrylic paint for the glossy finish. Finally 6/7 coats of wax alternating with polishing and you will have a perfect mould.
Before priming you will have to sand the inside of the mold to eliminate the marks of the printing layers...
Before priming you will have to sand the inside of the mold to eliminate the marks of the printing layers...
#8

The primer that I used is a two-component acrylic auto body primer. Two coats alternating with light sanding are sufficient. Then I used a two-component acrylic paint for the glossy finish. Finally 6/7 coats of wax alternating with polishing and you will have a perfect mould.
Before priming you will have to sand the inside of the mold to eliminate the marks of the printing layers...
Before priming you will have to sand the inside of the mold to eliminate the marks of the printing layers...
I used putty first and then something like a grey base before the paint. I don't like working with the putty since it gave me very short time and lots of sanding work
Thank you
#9

Thread Starter

What you see in gray is a spray-catalysed two-component filler applied with an air gun (3 coats). Sanding is quick and easy. After the gray stucco he gave a catalyzed two-component gloss varnish. Finally sinhy everything with polish...
#10

Which 3D printer do you use? I've read the article and still can't choose, but tend to Creality Ender 3, is it convenient?
#12
Junior Member
Join Date: Mar 2019
Posts: 21
Likes: 0
Received 0 Likes
on
0 Posts

Hi Sandro,
Nice work, I saw it and I am inspired to follow your way now :-)
Please can you give me some info?
- Where the fuel output fitting (you have used) can be obtained from?
- For those another brass fittings: did you use also the nut from the underside of it is just glued without nut? Did you use gaskets included (suppose no)
- Using your fabrics layer combination: is the tank transparent enough to see the rest of the fuel after flight?
- Is common lamination epoxy (MGS one with blue hardener) compatible with jet fuel? No degradation after some time?
Thanks much,
Richard
Nice work, I saw it and I am inspired to follow your way now :-)
Please can you give me some info?
- Where the fuel output fitting (you have used) can be obtained from?
- For those another brass fittings: did you use also the nut from the underside of it is just glued without nut? Did you use gaskets included (suppose no)
- Using your fabrics layer combination: is the tank transparent enough to see the rest of the fuel after flight?
- Is common lamination epoxy (MGS one with blue hardener) compatible with jet fuel? No degradation after some time?
Thanks much,
Richard
#13

Thread Starter

Hi Sandro,
Nice work, I saw it and I am inspired to follow your way now :-)
Please can you give me some info?
- Where the fuel output fitting (you have used) can be obtained from?
- For those another brass fittings: did you use also the nut from the underside of it is just glued without nut? Did you use gaskets included (suppose no)
- Using your fabrics layer combination: is the tank transparent enough to see the rest of the fuel after flight?
- Is common lamination epoxy (MGS one with blue hardener) compatible with jet fuel? No degradation after some time?
Thanks much,
Richard
Nice work, I saw it and I am inspired to follow your way now :-)
Please can you give me some info?
- Where the fuel output fitting (you have used) can be obtained from?
- For those another brass fittings: did you use also the nut from the underside of it is just glued without nut? Did you use gaskets included (suppose no)
- Using your fabrics layer combination: is the tank transparent enough to see the rest of the fuel after flight?
- Is common lamination epoxy (MGS one with blue hardener) compatible with jet fuel? No degradation after some time?
Thanks much,
Richard
Hi, I got the power fittings on Aliexpress. For fixing I used the nuts on the lower part (I mounted them before closing the two half-shells of the mold) and glued them on the external part. The tank made like this is not transparent but you can see the liquid inside...