Getting a feather trailing edge on foam cores
#1
Moderator
Thread Starter

I want to cut my own cores for a future SPA project. In my last build, the factory made cores where left with a flat TE that required adding a balsa TE and ailerons. I guess they did that because tapering the cores to a perfect sharp edge is hard to do? So do you guys have any tips for me on getting a sharp trailing edge with foam?
#2

My Feedback: (3)

The foam trailing edge is to fragile stick with the balsa one.
One of the university Aerodesign teams insisted on trying the tapered foam trailing edge and it never worked out with the hot wire cut. When they still insisted they tried cutting and shaping it and it turned out looking like poo. It didn't even come close to looking like the airfoil they were trying to duplicate.
Even molded airfoil are not usually feathered but end in a blunt edge
One of the university Aerodesign teams insisted on trying the tapered foam trailing edge and it never worked out with the hot wire cut. When they still insisted they tried cutting and shaping it and it turned out looking like poo. It didn't even come close to looking like the airfoil they were trying to duplicate.
Even molded airfoil are not usually feathered but end in a blunt edge
Last edited by Propworn; 01-06-2020 at 05:19 AM.
#3

Join Date: Sep 2007
Location: Beeton, Ontario, CANADA
Posts: 1,357
Likes: 0
Received 7 Likes
on
6 Posts

Philip Avonds is a well know championship builder and he says that the squared off TE is intentional so as to reduce flutter. I discovered this when building one of his F-104 kits. There is no other plane out there that deserves a feather edge more than the starfighter, but he insist it is not a good idea to have feathered TE's
#4
Moderator
Thread Starter

I'm doing sheeted foam wings, so a feather edge will yield a 1/8 inch thick TE when it's sheeted. I guess keeping 1/16 or so wouldn't be so bad, as I could sand the sheeting down a little to thin it.
#5

My Feedback: (29)

Jester, the best way to achieve what you are looking for is to make your templates in upper and lower halves. When cutting the wing this would allow you to adjust the thickness of the TE to whatever you want. Coming to a sharp edge TE with your foam will never be perfect but as you said it won't matter after being sheeted. Like you said it will be 1/8" at that point anyways. To get a really sharp TE, I bring the sheeting 1/4" past the core, cap with 1/8" square bass wood and sand to the desired sharpness. For some added durability you can add a strip of fiberglass cloth between the sheeting but only if you are using epoxy to adhere the sheeting to the cores. I have used this method on many pylon airplanes.
#8

My Feedback: (3)

I use .020 stainless mig wire a small roll will last you and your friends a lifetime. Its cheaper and the wire thickness and its content is highly controlled giving the best overall heat distribution. I clean/polish the wire with a piece of scotch bright pad for each cut. My bows range up to 9 feet and free hand with the wire attached at one end and held at the other just about any length is possible.
#9

I am sure what Jester was talking about is the two 1/16 wing skins come together, has a 1/8 inch trailing edge. Which is actually GOOD ! I cap my 1/8 inch trailing edge with hard balsa which reduces hangar rash on a sharp trailing edge.
I have build and cut many foam core with what is called "Feather edge". They make great ailerons when cut from they are cut from the core. It sure beats sanding two sticks to the
shape of ailerons which never match up to the wing.
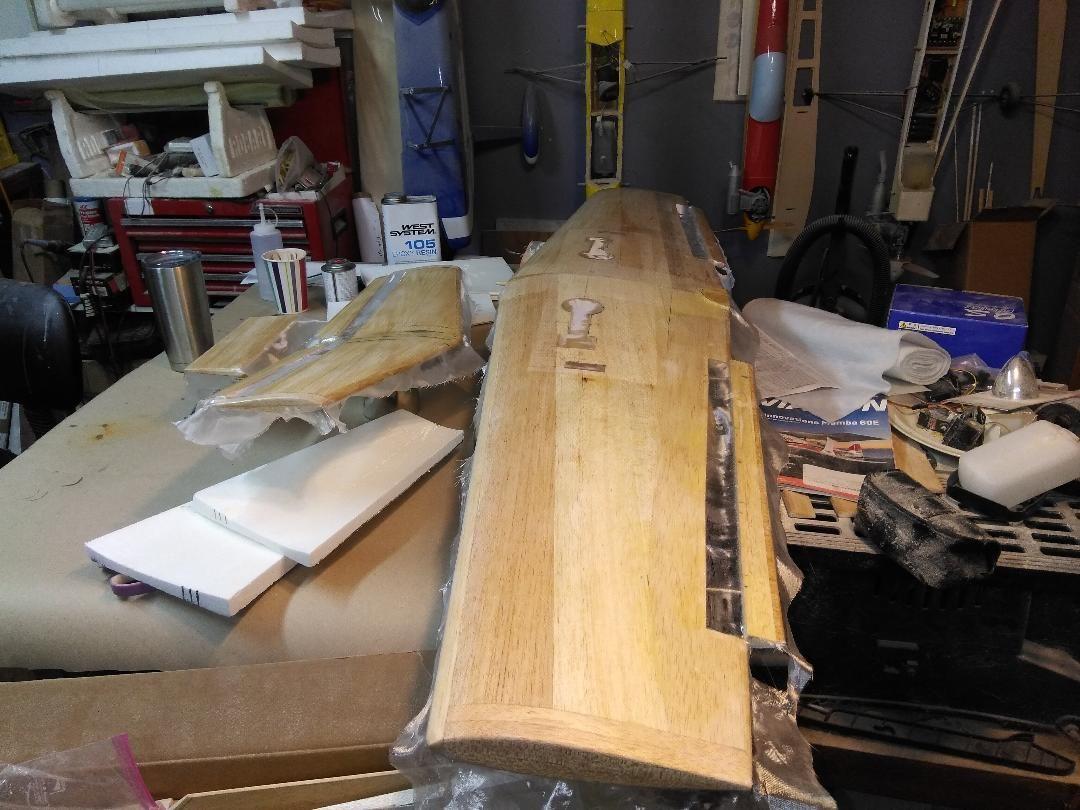
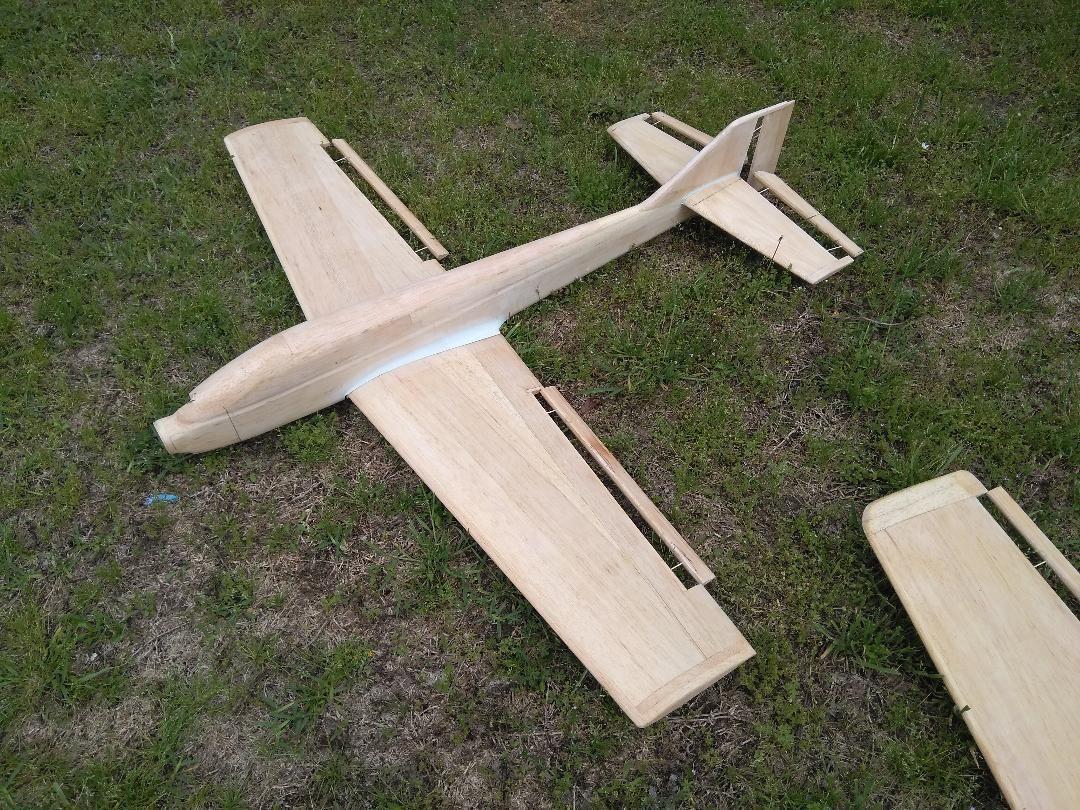

I have build and cut many foam core with what is called "Feather edge". They make great ailerons when cut from they are cut from the core. It sure beats sanding two sticks to the
shape of ailerons which never match up to the wing.
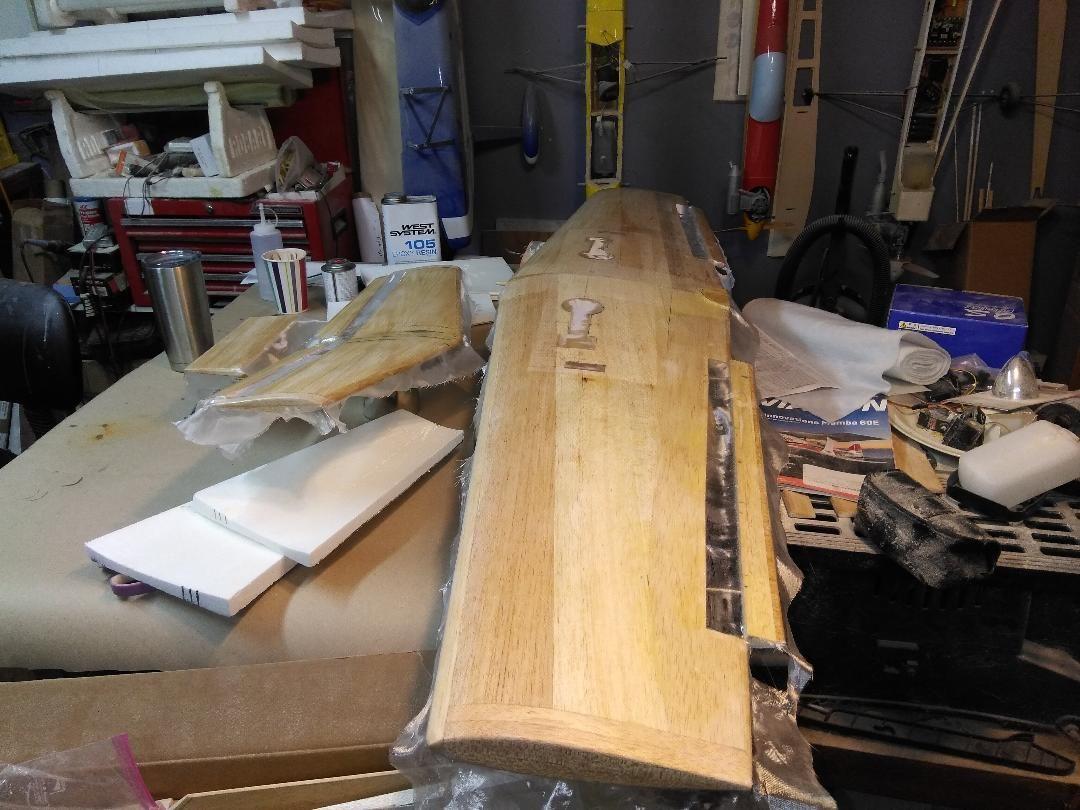
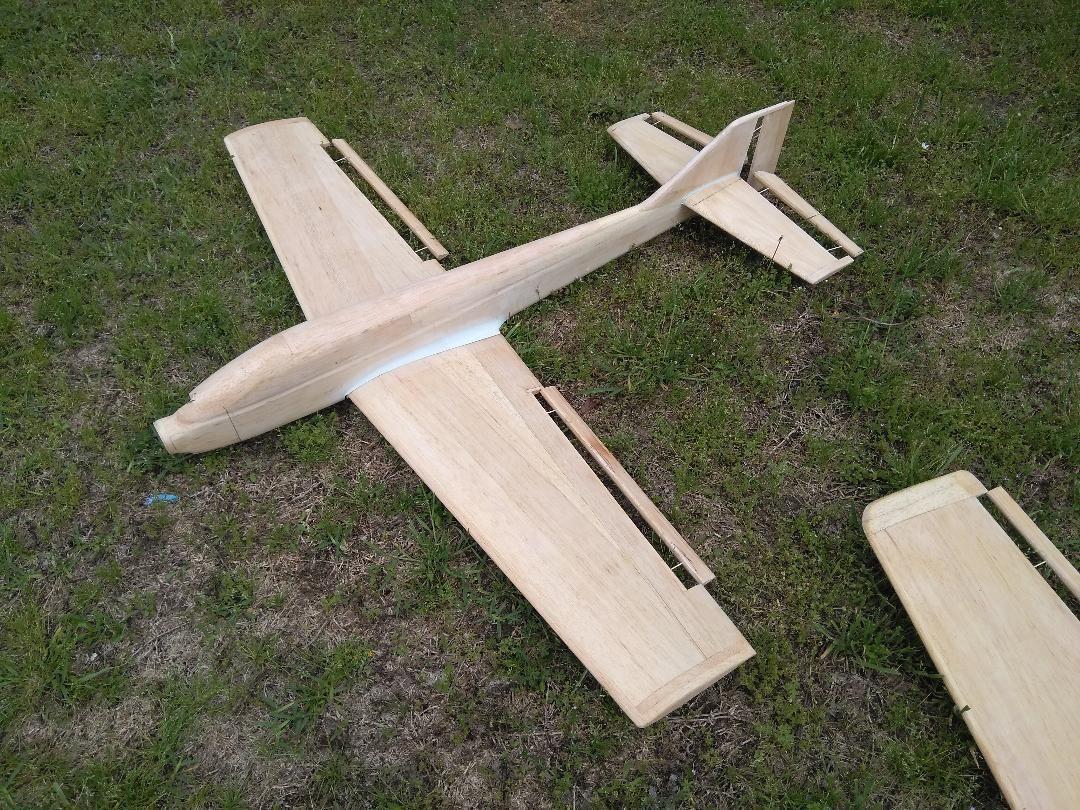

Last edited by countilaw; 05-12-2020 at 09:38 PM.
#11


While it may seem ideal to feather the trailing edge of a foam core, I don't see it as a necessity (assuming that your intention is to end up with a sharp finished trailing edge). What you really need to account for is the dimension of the final outline because after balsa sheeting, your trailing edge will extend a quarter inch or more past the trailing edge of the foam where the upper and lower skins come together with a beveled joint.
To put it another way, throughout the wing the balsa skin is guided by the foam, but at last part of the trailing edge it is the skin that determines the shape or contour of the skin at the joint because it becomes all balsa for a quarter inch or more (balsa to balsa).
To put it another way, throughout the wing the balsa skin is guided by the foam, but at last part of the trailing edge it is the skin that determines the shape or contour of the skin at the joint because it becomes all balsa for a quarter inch or more (balsa to balsa).
#12
Moderator
Thread Starter

I didn't mean that I wanted a super sharp training edge. I am looking to do what Countilaw did,
So how 'bout it ol friend? Any tips on not winding up with a wavy TE when I try to get it that thin?
So how 'bout it ol friend? Any tips on not winding up with a wavy TE when I try to get it that thin?
#13


It's not clear to me what kind of "wavy" you're getting or trying to avoid. Even more confusing is that you indicate that you are not looking to do a super sharp trailing edge, but at the same time asking how to avoid a wavy trailing edge, as you say, "...when I try to get it that thin".
If you're not looking for a sharp trailing edge, why would you be trying to get it "that thin"?
#14


Maybe if you post a picture of the problem you're having, perhaps someone with experience in that specific area can advise you.
Personally, I don't seem to have a clue about the nature of the difficulty.
Personally, I don't seem to have a clue about the nature of the difficulty.
#15

My Feedback: (29)

My Divergent build has good info on sheeting wings. The current trend is to have blunt trailing edges but I have used the same technique when I was flying pylon. As Steve states you cut the core to a sharp TE, it will look terrible but it won't matter. The wing sheeting will be cut 1/4" past the foam TE. A few options here, you can add a 2" strip of 1.4oz fiberglass cloth on the sheeting TE or cut 1/8" off the core TE and after the lower sheeting is in place with the 1/4" overlap apply some 20K CF tow that has been wet out with resin. Of course you could do both. When dry you would be able to sand to a 1/32" thick TE that will be quite durable.
https://www.rcuniverse.com/forum/ele...gent-kits.html
https://www.rcuniverse.com/forum/ele...gent-kits.html
#16
Moderator
Thread Starter

What I meant was I don't mean to wind up with a sharp TE when the wing is all sheeted. Skinning with 1/16 balsa on a feathered TE core will yield a 1/8 TE before sanding. That seems to work pretty well.
I had not thought about what speedracerntrixie said with allowing some space for a different sandwich material. Maybe I'll go that route on my next build.
I had not thought about what speedracerntrixie said with allowing some space for a different sandwich material. Maybe I'll go that route on my next build.