airframe temperatures
#1

Thread Starter
Join Date: Nov 2014
Posts: 106
Likes: 0
Received 0 Likes
on
0 Posts

hi curently looking for a nice epoxy laminating resin for my f-14 fiberglass fuse projet and was wondering how hot does it get in there with twin turbines. im trying to figure out if i should go with a high temperature laminating resin that needs to be oven baked for full result or just go with regular laminating resin and air cure it like normal.
#2


I just line the inside of the areas exposed to high heat with aluminum tape. In the past, I have also used BVM's paint on Heat Shield but it is heavier. But, the heat is generally moved out by motion forward. When must of us that are worried about heat build up during and after shutdown, we use small leaf blowers until the jet stops it's cooldown cycle.
#3
#5

Thread Starter
Join Date: Nov 2014
Posts: 106
Likes: 0
Received 0 Likes
on
0 Posts

does it sand easy? do i need to vaccum bag it? i have a fiberglassed wood plug of the plane now ready was planning on putting two sglass layers in top of it with the mold release and then just cut it half on the horizontal to free the mold and then glue back both halfs
#6


hi curently looking for a nice epoxy laminating resin for my f-14 fiberglass fuse projet and was wondering how hot does it get in there with twin turbines. im trying to figure out if i should go with a high temperature laminating resin that needs to be oven baked for full result or just go with regular laminating resin and air cure it like normal.
Oli helped me tremendously:
1) My exhaust pipes were single wall, Oli made them double - with very thin gap, 4-5mm between inner and outer skin allowing the air in between the skins to act as an insulator. And as we know from physics, air is the best insulator of all.
2) he provided me with this fantastic product https://www.ultimate-jets.net/produc...eramic-blanket to cover the inner part of the fuselage, extremely light and easy to apply - very easy and especially very easy on curved surfaces. laminating epoxy will possibly add more weight to your airframe than this blanket.
Thanks Oli
The result? maybe 50C difference in temps on the fus skin, maybe more, but great help - problem solved.
Thanks, Tassos
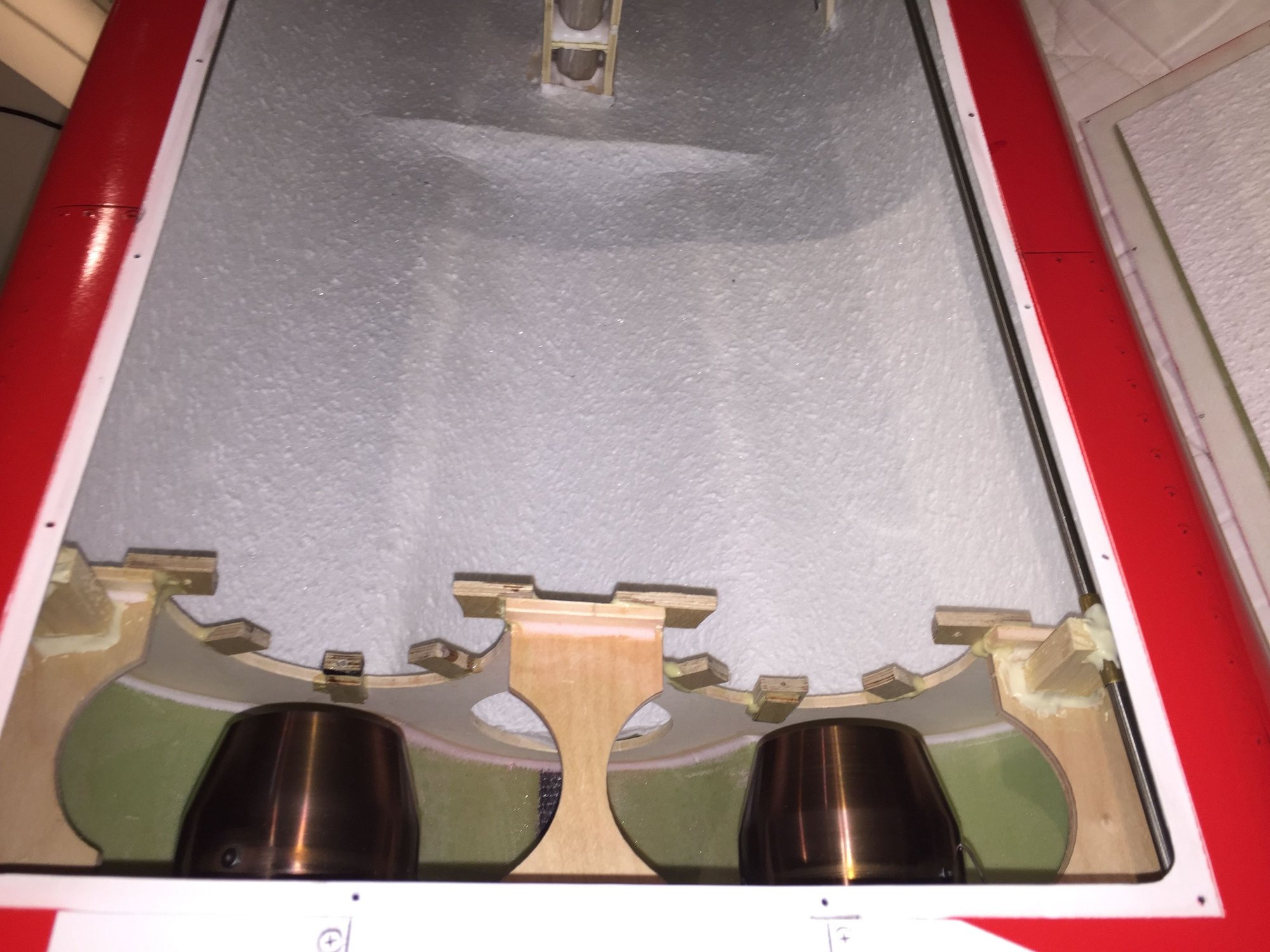
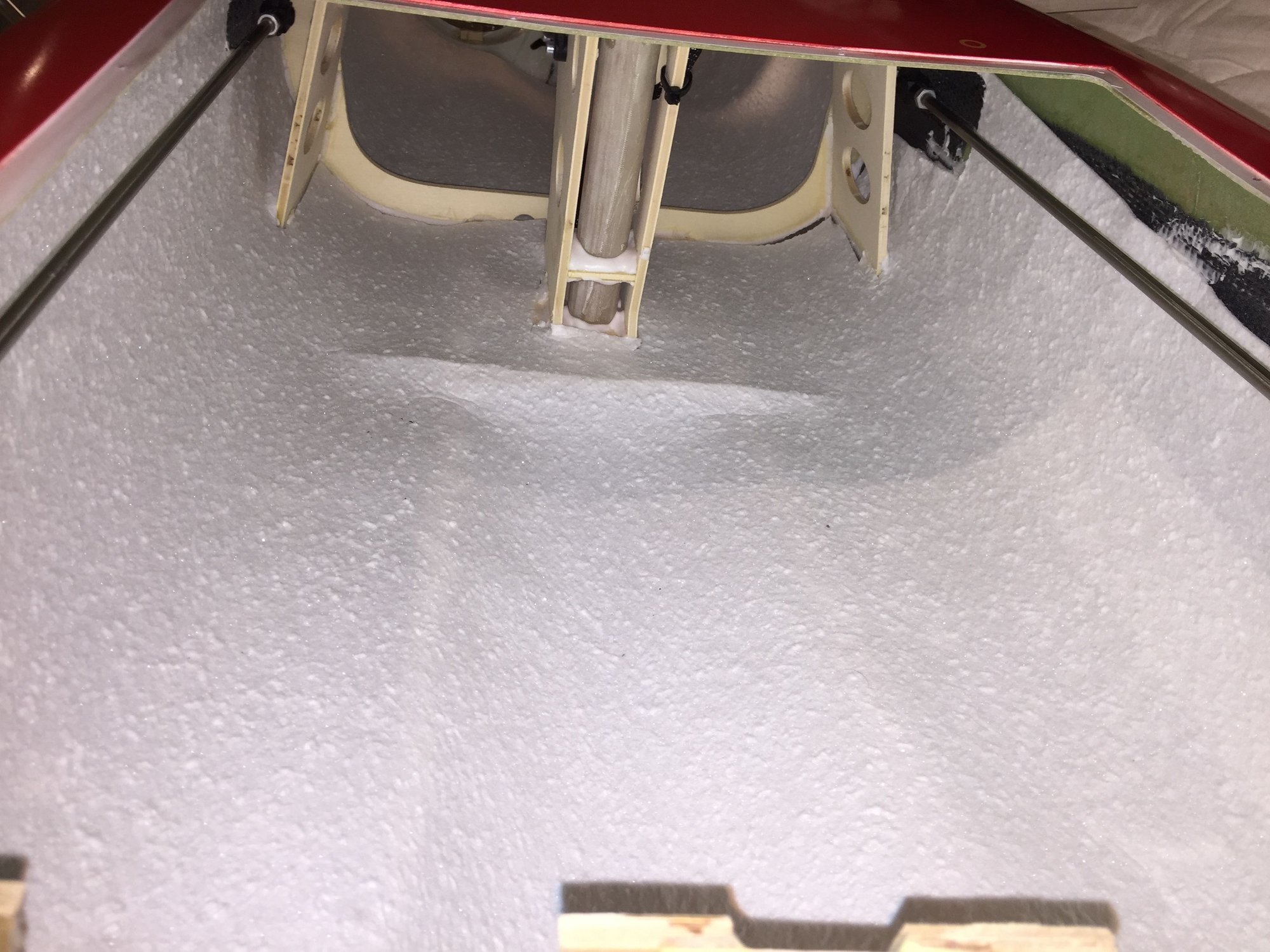
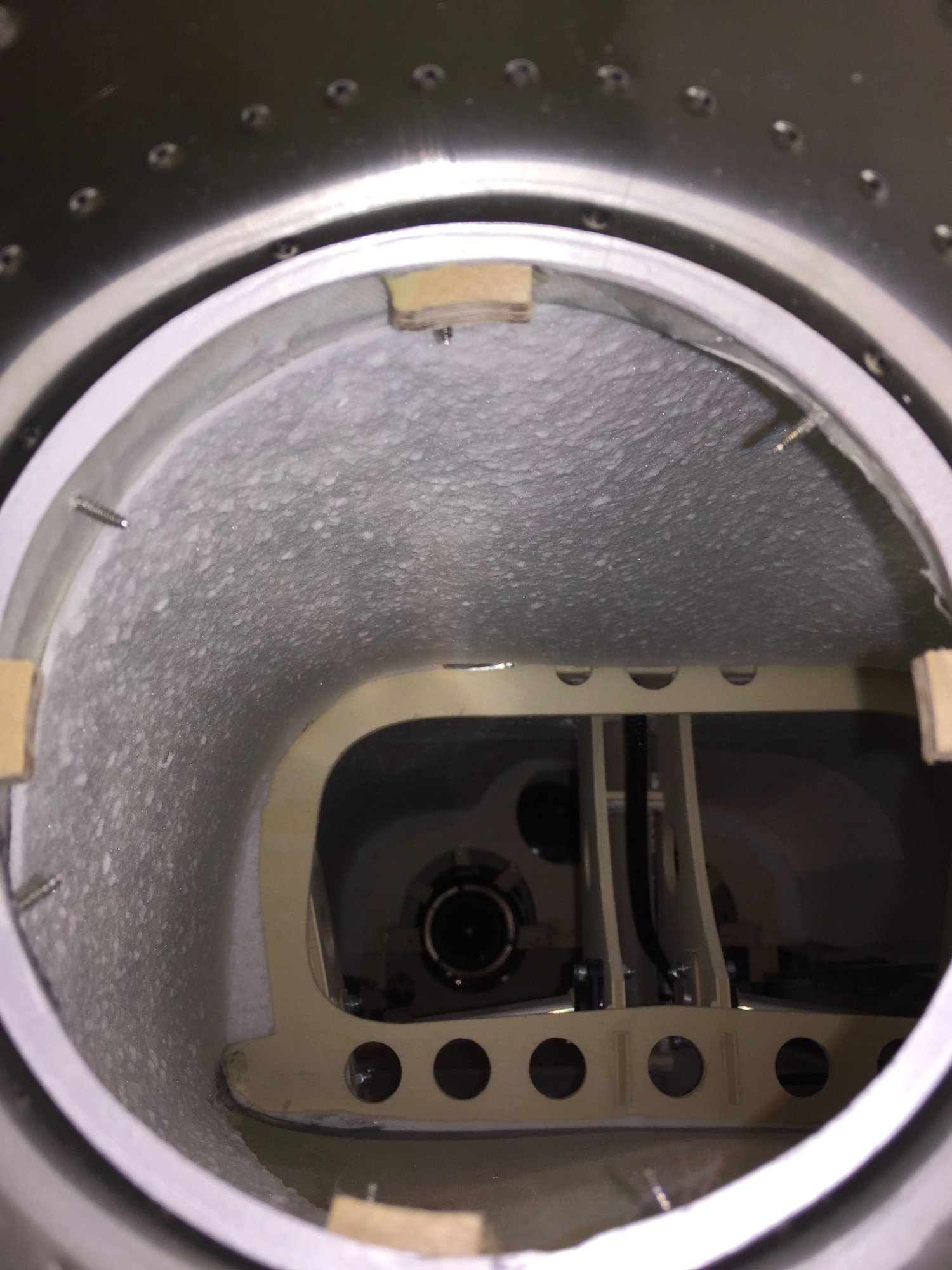
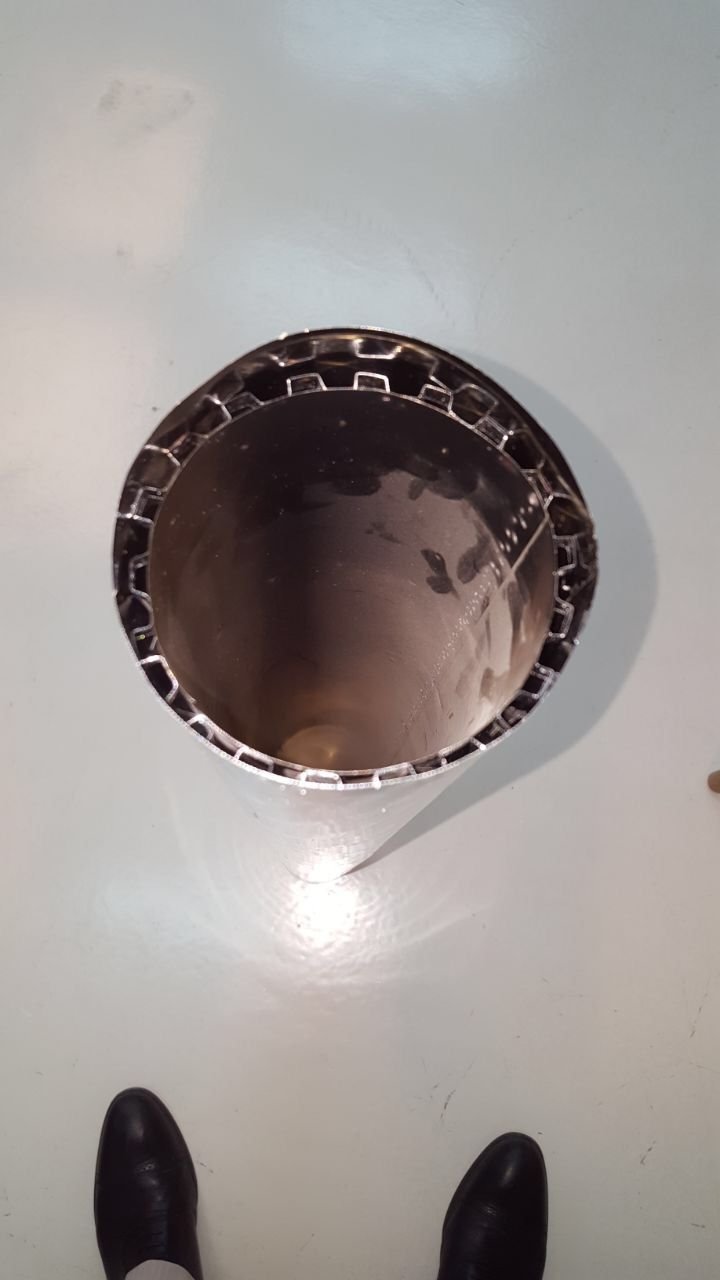
#7

You're welcome, Tassos.
We have accumulated a considerable experience on heat management with our aerospace contracts.
We are working with carbon/ PMR-15 polyimide pre-pregs and carbon-carbon materials for some projects and I will possibly step down some of this technology to the hobby market at some point.
I wrote the article above to pass this experience on to the community.
It's always a pleasure to help fellow modelers and friends.
We have accumulated a considerable experience on heat management with our aerospace contracts.
We are working with carbon/ PMR-15 polyimide pre-pregs and carbon-carbon materials for some projects and I will possibly step down some of this technology to the hobby market at some point.
I wrote the article above to pass this experience on to the community.
It's always a pleasure to help fellow modelers and friends.
#8

Thread Starter
Join Date: Nov 2014
Posts: 106
Likes: 0
Received 0 Likes
on
0 Posts

cool thanx for the info looking for the best product to deal with the heat especially here being a twin turbine application. the main concern is because i plan on using in house develloped working afterburners the heat will be a serious issue so im looking for the best product to deal with the heat without beiing on the heavy side.
#9

Thread Starter
Join Date: Nov 2014
Posts: 106
Likes: 0
Received 0 Likes
on
0 Posts

question here for Oli is what is the rated performance temp wise on those double walled exhaust pipes. stainless steel afterburner cans are mounted behind the turbine with airbypass and ring igniter with variable nozzle. airframe is two sglass layers with hight temp epoxy 500•F rated performance so id be happy to discuss materials and eventually pricing for twin turbine exhaust pipes applications
#10

We are using austenistic steel rated at 1400 F maximum service temperature. However, the main limiter here would be the rigidity of your pipe wall.
A/B create a massive amount of vacuum when accelerating the mass flow, while generating a lot of radiant heat. The risk of pipe collapsing is a very high with thin walled non ribbed ducts.
A/B ducts are usually ribbed on full size aircraft for this reason.
I would seriously consider a ceramic coated carbon/ BMI compposite duct in this application.
However, budget might be a concern, as these pre-preg need autoclave curing at 700 F, then post curing at 1500 F.
We mostly make these for military/ rocket applications...
A/B create a massive amount of vacuum when accelerating the mass flow, while generating a lot of radiant heat. The risk of pipe collapsing is a very high with thin walled non ribbed ducts.
A/B ducts are usually ribbed on full size aircraft for this reason.
I would seriously consider a ceramic coated carbon/ BMI compposite duct in this application.
However, budget might be a concern, as these pre-preg need autoclave curing at 700 F, then post curing at 1500 F.
We mostly make these for military/ rocket applications...
#11

Thread Starter
Join Date: Nov 2014
Posts: 106
Likes: 0
Received 0 Likes
on
0 Posts

how much for two of those pipes for 1/10 f14 application? AB will be used briefly on takeoff and for couple seconds on low passes so the heat is not continous but i still want things arround to remain in the unmelted state so i might go in that direction if it doesnt cost too much but i also understand its hi grade material/fabrication here so i guess ill keep my wallet close by.
#12

Thread Starter
Join Date: Nov 2014
Posts: 106
Likes: 0
Received 0 Likes
on
0 Posts

tell me more about the process of manufactring a piece like this with the materials involved. if you have a website for your company i can read about this high tech stuff and understand it better before dishing out top dollars. im new to rc jets this would be my first jet model and im learning a lot of new things as i progress in my project. i like to build kits i dont buy arfs never have never will the fun is learning and building and when u fly it at a meet it makes great knowledgable conversations.
#13

Well, an afterburner system is integral of the engine. It is not a thrust tube that is placed behind the jet pipe.
It is a cone replacement that bolts onto the engine.
Because the airflow is significantly increased through the engine, the fuel mapping has to be changed. This requires an ECU with 2 maps. One "dry" and one "wet".
The injection nozzles are in the custom pipe and require custom turbulators to stabilize the flame. Variable section exhaust is pretty much required as well .
The pipe itself can be made of austenistic steel / inconel ( heavy ) or carbon/ BMI prepregs.
The latter requires an aluminum mold.
The pre-preg is pressure molded at 700 F. The levels of pressure required are very high and require a special autoclave.
Once the curing cycle is finished, a post-curing cycle is required for several hours until 1500 F. The curing and post-curing ramps are critical and typically of 3 F per 20 min with holding periods of several hours.
This requires an industrial oven.
The carbon/ BMI pre-preg is typically in the region of 20 k USD per roll. MOQ is usually 3 to 5 rolls.
A typical manufacturing batch is for 30 to 50 parts.
Contracts include manufacturing material, machines costs as well as mold manufacturing, designs and a pletora of non recurring fees including those for AS 9100D or MIL-Q-9858 processes.
This material is restricted and will not be sold to a hobby manufacturer.
All of these involve proprietary designs for military or aerospace purposes.
Note that A/Bs on RC models are illegal in the USA.
It is a cone replacement that bolts onto the engine.
Because the airflow is significantly increased through the engine, the fuel mapping has to be changed. This requires an ECU with 2 maps. One "dry" and one "wet".
The injection nozzles are in the custom pipe and require custom turbulators to stabilize the flame. Variable section exhaust is pretty much required as well .
The pipe itself can be made of austenistic steel / inconel ( heavy ) or carbon/ BMI prepregs.
The latter requires an aluminum mold.
The pre-preg is pressure molded at 700 F. The levels of pressure required are very high and require a special autoclave.
Once the curing cycle is finished, a post-curing cycle is required for several hours until 1500 F. The curing and post-curing ramps are critical and typically of 3 F per 20 min with holding periods of several hours.
This requires an industrial oven.
The carbon/ BMI pre-preg is typically in the region of 20 k USD per roll. MOQ is usually 3 to 5 rolls.
A typical manufacturing batch is for 30 to 50 parts.
Contracts include manufacturing material, machines costs as well as mold manufacturing, designs and a pletora of non recurring fees including those for AS 9100D or MIL-Q-9858 processes.
This material is restricted and will not be sold to a hobby manufacturer.
All of these involve proprietary designs for military or aerospace purposes.
Note that A/Bs on RC models are illegal in the USA.
Last edited by olnico; 01-11-2019 at 05:39 PM.
#14

Here is the kind of problem you'd get by using standard SS for the afterburner section.
Pretty much self destroys after a couple of tests.
Here is the Russian design that works a bit better ( at -40c OAT ):
Overall, you need materials with service temperatures of 1500 F.
There were a couple of flight demos at Jet Power on the last 2 years, which I did not enquier.
Pretty much self destroys after a couple of tests.
Here is the Russian design that works a bit better ( at -40c OAT ):
Overall, you need materials with service temperatures of 1500 F.
There were a couple of flight demos at Jet Power on the last 2 years, which I did not enquier.
Last edited by olnico; 01-11-2019 at 05:31 PM.
#16

My Feedback: (40)

Here is the kind of problem you'd get by using standard SS for the afterburner section.
Pretty much self destroys after a couple of tests.
https://www.youtube.com/watch?v=ACENMajlZ-8
Here is the Russian design that works a bit better ( at -40c OAT ):
https://www.youtube.com/watch?v=s2_tXIVebJI
Overall, you need materials with service temperatures of 1500 F.
There were a couple of flight demos at Jet Power on the last 2 years, which I did not enquier.
Pretty much self destroys after a couple of tests.
https://www.youtube.com/watch?v=ACENMajlZ-8
Here is the Russian design that works a bit better ( at -40c OAT ):
https://www.youtube.com/watch?v=s2_tXIVebJI
Overall, you need materials with service temperatures of 1500 F.
There were a couple of flight demos at Jet Power on the last 2 years, which I did not enquier.
#17

My Feedback: (54)

One of the things that I have been curious is to, other then the cost. Why not use triple wall pipe? With the smaller jets, I get the room issues, but with the twins and the large jets, I would think triple wall would work. Seems to work well with wood burning stoves. With them, you can touch the outside pipe with the stove burning as hot as you can get it. It's just an extra sleeve of pipe and accordian spacers.